Abstract
In this paper, a computer simulation of a high-pressure die casting of aluminum alloy was performed using a commercially available software and also compared with the real castings of the same alloy. The commercial aluminum alloy was Etial 150 (AlSi12Cu) that is used for flange which is a washing machine part. Mold filling, solidification, temperature distribution, porosity, and velocity of the liquid metal during high-pressure die casting were investigated using the model through numerical simulation. The simulation results proved that the model values used in simulations were accurate in order to apply for experimental casting. After this numerical model, the flange part was cast experimentally according to the obtained optimum parameters from simulation results. Then, specimens from the experimental casting were tested for tensile, hardness, and microstructure analyses. Accordingly, the test results are rather sound which demonstrates that simulation provides profitable die casting. Consequently, it was observed from this study that simulation is not only useful for enhancing casting quality but also very economical and practical, which helps to reduce time spent on experiments. Moreover, simulation can reveal porosity and helps to minimize this defect. Thus, computer simulation should be used for casting applications more often, and simulation programs should be developed further.


























Similar content being viewed by others
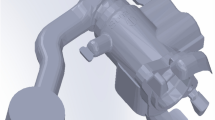
References
Z. Guo, N. Saunders, J.P. Schillé, A.P. Miodownik, Modelling of materials properties and behaviour critical to casting simulation. Mater. Sci. Eng. A 413–414, 465–469 (2005)
J.R. Brown, in Foseco Ferrous Foundryman’s Handbook, 11th edn. pp. 222–226 (2000)
P. Beeley, in Foundry Technology, 2nd edn. pp. 449–467 (2001)
C. Døruma, H.I. Laukli, O.S. Hopperstad, Through-process numerical simulations of the structural behaviour of Al–Si die-castings. Comput. Mater. Sci. 46(1), 100–111 (2009)
P. Kennedy, R. Zheng, in Flow Analysis, 2nd edn. pp. 3–11 (2013)
S. Yue, G. Wang, F. Yin, Y. Wang, J. Yang, Application of an integrated CAD/CAE/CAM system for die casting dies. J. Mater. Process. Technol. 139, 465–468 (2003)
P.K. Seo, D.U. Kim, C.G. Kang, The effect of the gate shape on the microstructural characteristic of the grain size of Al–Si alloy in the semi-solid die casting process. Mater. Sci. Eng. A 445, 20–30 (2007)
K. Domkina, J.H. Hattela, J. Thorborg, Modeling of high temperature- and diffusion-controlled die soldering on aluminum high pressure die casting. J. Mater. Process. Technol. 209, 4051–4061 (2009)
P.W. Cleary, J. Ha, M. Prakash, T. Nguyen, 3D SPH flow predictions and validation for high pressure die casting of automotive components. Appl. Math. Model. 30, 1406–1427 (2006)
P. Cleary, J. Ha, V. Alguine, T. Nguyen, Flow modelling in casting processes. Appl. Math. Model. 26, 171–190 (2002)
P.W. Cleary, J. Ha, Three-dimensional smoothed particle hydrodynamics simulation of high pressure die casting of light metal components. J. Light Met. 2, 169–183 (2002)
P. Homayonifar, R. Babaei, E. Attar, S. Shahinfar, P. Davami, Numerical modeling of splashing and air entrapment in high-pressure die casting. Int. J. Adv. Manuf. Technol. 39(3/4), 219–228 (2008)
J.J. Hernández-Ortega, R. Zamora, P. Julián, J. López, F. Faura, Experimental and numerical study of air entrapment during the filling of a mould cavity in die casting, in AIP Conference Proceedings, vol. 907, issue 1, pp. 1430–1435 (2007)
H. Rafii-Tabar, A. Chirazi, Multi-scale computational modelling of solidification phenomena. Phys. Rep. 365(3), 145–249 (2002)
K.M. Pedersen, N. Tiedje, Temperature measurement during solidification of thin wall ductile cast iron. Part 2: numerical simulations. Measurement 41, 341–348 (2008)
H.V. Atkinson, Modelling the semisolid processing of metallic alloys. Prog. Mater Sci. 50(3), 341–412 (2005)
P.W. Cleary, J. Ha, M. Prakash, T. Nguyen, Short shots and industrial case studies: understanding fluid flow and solidification in high pressure die casting. Appl. Math. Model. 34(8), 2018–2033 (2010)
S.V. Shepel, S. Paolucci, Numerical simulation of filling and solidification of permanent mold castings. Appl. Therm. Eng. 22(2), 229–248 (2002)
J.W. Bae, D.Y. Seol, C.G. Kang, S.M. Lee, Die life prediction considering thermal fluid flow and solidification phenomenon in rheology process. J. Mater. Process. Technol. 201, 336–341 (2008)
Author information
Authors and Affiliations
Corresponding author
Technical Review and Discussion
Technical Review and Discussion
A Numerical and an Experimental Investigation of a High-Pressure Die Casting Aluminium Alloy
Özlem Boydak; Istanbul Medeniyet University, Istanbul, Turkey
Mahmut Savaş; Yakın Doğu University, Lefkoşa, KKTC
Bulent Ekici; Marmara University, Istanbul, Turkey
Reviewer:
Why steady state is always achieved in 5 cycles regardless of the geometry? What if the casting is thicker or thinner?
Authors:
Five cycles of casting are needed in order to perform a realistic simulation since five cycling provides heating the mould completely. And proper mould heating is crucial for high-pressure die casting. The simulations having less than five cycles cannot heat the mould completely, and then, the simulation becomes less realistic for the casting application. For instance, if the simulation is done with one cycle instead of five cycles, an ideal simulation result cannot be obtained since the mould is not heated enough. Five cycling is only related to proper mould heating and not related to the part geometry, size, shape and thickness.
Reviewer:
The authors state that since the temperature is uniform, the solidification would be uniform. This seems to be challenged later in the paper (in Sect. 3.3 and again in 3.6). Please clarify.
Authors:
The temperature results in Sect. 3.2 are consistent with the results in Sects. 3.3 and 3.6 . The unfavourable parts observed in Sects. 3.3 and 3.6 are both negligible, and they are not in the major casting part. There are hot spots in Sect. 3.6 . However, the levels of these hot spots are not dangerous and they are not permanent. Therefore, it can be accepted as uniform. Accordingly, a homogeneous pressure distribution is observed from Sect. 3.3 and there is only pressure change in the overflows, but this is not crucial since this area of overflows will be cut off after the solidification.
Reviewer:
The conclusion states that a minimum of 5 cycles are needed. Is that for a part of this size and shape? Is this all castings in general? Can you provide validation?
Authors:
The simulation results done with 5 cycles give the most realistic values according to the experiences from the other simulations done up to the present, because the mould is heated sufficiently by five cycling as the real casting application, and thus, the real-like optimum values are obtained. Therefore, the simulations are in general recommended to be done with at least five cycling according to the prior experiences of the simulation programme for all high-pressure die casting parts not concerning the sizes and shapes of the parts.
Reviewer:
The simulation results still show significant porosity in the biscuit area. This does not match the tensile specimen data that were presented.
Authors:
There is porosity in biscuit, but there is negligible porosity in the major casting part. Besides, biscuit will be cut and discarded after solidification and the major casting part will be utilized. Therefore, the porosity seen in the biscuit part does not affect the casting quality. Thus, the testing data are compatible with the simulation data.
Rights and permissions
About this article
Cite this article
Boydak, Ö., Savaş, M. & Ekici, B. A Numerical and an Experimental Investigation of a High-Pressure Die-Casting Aluminum Alloy. Inter Metalcast 10, 56–69 (2016). https://doi.org/10.1007/s40962-015-0004-4
Published:
Issue Date:
DOI: https://doi.org/10.1007/s40962-015-0004-4