Abstract
Glass fiber reinforced polymer (GFRP) composites have high sensitivity to UV radiation, temperature, and moisture, and these factors lead to the decrease of mechanical properties. This study attempts to modify unsaturated polyester (UP) and vinylester (VE) resins with nano zinc oxide (ZnO) and organo-montmorillonite (OMMT), in order to improve UV radiation resistance and hygrothermal resistance. The nano ZnO/OMMT modified UP and VE based GFRP composites were subjected to UV radiation and hygrothermal aging at 30 °C, 50 °C and 60 °C (95% RH) for 90 days. Mass loss, moisture uptake, color change, flexural properties and short-beam-shear test were investigated. In comparison to unmodified GFRP specimens, ZnO/OMMT modifying decreased the mass loss, the color change, saturation moisture uptake, and the coefficient of diffusion. After exposure in UV radiation for 90 days, the flexural strength and interlaminar shear strength of nano modified GFRP composites increased by 23.5% and 27.8% compared with those of the unmodified GFRP composites. Nano ZnO/OMMT modifying also increased the flexural strength and interlaminar shear strength by 26.5% and 27.2% in hygrothermal condition at 60 °C. Furthermore, based on the change of mechanical properties and Arrhenius rate model, a prediction model was proposed to predict the life of nano modified FRP composites.
Export citation and abstract BibTeX RIS

Original content from this work may be used under the terms of the Creative Commons Attribution 4.0 licence. Any further distribution of this work must maintain attribution to the author(s) and the title of the work, journal citation and DOI.
1. Introduction
Fiber reinforced polymer (FRP) composites have been widely used in aerospace, submarines, underwater pipelines, automobiles, and building components [1, 2] due to their improved strength at small specific weight, ease of design and installation [3, 4]. These ever-increasing applications of FRP composites demand lifetimes of 15, 25, 50, and even 100 years. However, during their service life, FRP composites are inevitably exposed to harsh environments which involve elevated temperature and moisture including ultraviolet (UV) radiation.
To understand the changes in material properties due to environmental effects, researchers investigated mechanical properties and long-term durability of FRP composites under different harsh environments [5]. UV radiation is known to have negative effects on most polymers, as it promotes mechanical and photochemical degradation reactions [6]. Correia et al [7] investigated UV effects on pultruded FRP composites. They found that UV mainly resulted in gloss loss and a change in color (surface yellowing). Further experimental study was conducted by Sousa et al [8]. They reported that the tensile strength of glass fiber reinforced polymer (GFRP) profiles made of unsaturated polyester (UP) and vinylester (VE) decreased by 21% and 3% after 3000 h of artificial accelerated aging weathering chamber (QUV) exposure, respectively. They also found that tensile modulus presented analogous results, although a higher degradation level was observed compared to tensile strength (33% and 24% of modulus loss for UP and VE profiles, respectively). The results indicated that UP profiles presented lower mechanical properties and stability to degradation compared with VE profiles. Yan et al [9] indicated that the tensile strength and modulus of flax fabric reinforced epoxy composites decreased 30% and 35%, respectively, under the combined effect of ultraviolet (UV) radiation and water spraying. Uomoto et al [10] found that the tensile strength of GFRP decreased by 18.8% after 3 years of sunlight exposure. Ashrafi et al [11] studied the physical processes that governed polymer and fiber/matrix interface degradation by examining FRP specimens subjected to UV radiation under scanning electron microscopy (SEM). The results indicated that specimens subjected to UV radiation and condensation conditions revealed microcracks in the matrix. In addition, the hygrothermal condition, defined as an environment with combined moisture and elevated temperature, is supposed to be the severest environmental condition to cause swelling, plasticization, and degradation of the matrix, which degrades the performance of FRP composites [12, 13]. The influence of moisture absorption and temperature on mechanical properties of FRP composites has been documented in literatures [14–16]. Chu et al [14] investigated the tensile properties of GFRP profiles made of VE after immersion in deionized water at different temperatures. After immersion for 75 weeks, the tensile strength decreased 34.8% at 23 °C and 71.8% at 80 °C, respectively. Similar observations were made by Grammatikos et al [15] in which the tensile strength and in-plane shear strength were affected by hygrothermal aging. The tensile strength and n-plane shear strength of UP based GFRP profiles reduced by 16% and 31%, respectively, after 224 days immersed in distilled water at 80 °C. Furthermore, Tam et al [16] investigated the effect of hygrothermal conditioning on carbon fiber/epoxy interface by molecular dynamics simulation. They found that the interfacial adhesion decreased by as much as 78% in saltwater at high-temperature. Hence, it is necessary to enhance the mechanical properties of FRP composites under both UV radiation and hygrothermal conditions.
Up to now, many approaches for enhancing the mechanical properties of FRP composites have been investigated by the addition of montmorillonite (MMT) clay, silica (SiO2), alumina (Al2O3), silicon nitride (Si3N4), mica, zinc oxide (ZnO), titanium dioxide (TiO2), carbon nanotube, and so on. Gupta et al [17, 18] found that water diffusivity decreased to half its value in the neat resin when the clay content was only 1 wt%, whereas the reduction in water diffusivity was almost 91% when the clay content was 5 wt%. Addition of nanoclay influenced the diffusion behavior due to its high surface area and aspect ratio [19]. The diffusing water molecules have to travel around the flakelike barriers, and thus the addition of nanoclay into the matrix can decrease the diffusivity. Firdosh et al [20] also found that permeability and diffusivity decreased by 11% and 28% respectively with the addition of nanoclay. This can be attributed to clustering of water molecules in the vicinity of stacks of platelets. And thus water molecular path is altered, resulting in preventing the diffusion of water molecules into the matrix [21]. Zainuddin et al [22] investigated the effects of accelerated aging conditions on the mechanical properties of MMT clay filled epoxy composites. They observed that 2 wt% nanoclay reinforced composites conditioned at room temperature showed 7% and 38% increase in strength and modulus over neat specimens when similarly conditioned. In addition, 2 wt% nanoclay reinforced composites conditioned under hot-wet (80 °C) for 90 days showed 20% and 29% increase in strength and modulus over neat specimens when similarly conditioned. Similar results were obtained by Firdosh et al [20] in which specimens with 4 wt% nanoclay showed better strength retention than those of other specimens with lesser clay loading. Furthermore, Won et al [23] fabricated nano-GFRP rebar using SiO2, Al2O3, and Si3N4 nanomaterials. The nano-GFRP rebars immersed in alkaline solution for 115 days showed higher residual strength and smaller decreases in the strength ratio than the control GFRP rebars. The enhancement of the mechanical properties was attributed to enhanced durability and chemical stability of the nanoparticles, and blocking of the alkaline solution penetration by the nanoparticles. Robert et al [24] investigated the effect of the addition of modified mica on FRP properties. They found that the addition of 3% of 3-aminopropyltriethoxysilane (APS)- or octyldecylamine (ODA)-mica leaded to an increase of ∼25% of the ultimate tensile strength, and an increase of 27% and 29% of the tensile modulus of elasticity for APS- and ODA-mica, respectively. Gull et al [25] indicated that flexural strength and modulus of 3 wt% zinc oxide (ZnO) filled glass fiber reinforced polyester composites were increased by 188% and 422%, respectively, in comparison to unfilled composite. Prasad et al [26] conducted interlaminar fracture toughness testing of FRP composites with 0.5 wt% nano titanium dioxide (TiO2) and reported a 73% increase in mode I and mode II interlaminar fracture toughness values over the baseline FRP composites. A study conducted by Garg et al [27] reported that the mechanical performance of amino-functionalized nanotubes GFRP composites had a better response to the seawater aging environment as compared to both GFRP and pristine nanotubes GFRP composites when exposed to same conditions and aging duration. In addition, Phong et al [28] found that with an addition of core-shell rubber nanoparticles to epoxy matrix, the fatigue life of carbon fiber reinforced epoxy composites increased 75–100 times longer than that of the unmodified composites at high cycle fatigue.
As described above, nanoparticles have attracted much attention as good reinforcement candidates to improve mechanical properties of FRP composites. However, to the best of our knowledge, there is little information on a facile method to enhance the durability of FRP composites under both UV radiation and hygrothermal conditions. It is clear that MMT clay can provide barrier to moisture and enhance the crosslinking in polymers with increase in temperature [13]. In addition, zinc oxide is one of inorganic UV absorbers, and it can absorb light that matches or passes their band gap energy, which lies in the UV range of the solar spectrum [29, 30]. Hence, in this study, GFRP composites modified with nano ZnO and MMT clay were fabricated to enhance the durability under both UV radiation and hygrothermal conditions. The main objective of the present study is to investigate the effect of UV radiation and hygrothermal conditions on the durability of ZnO/MMT modified GFRP composites. Additionally, an analytical model depended on Arrhenius rate model, considered the effect of hygrothermal aging and UV radiation, was developed to predict the long-term performance of ZnO/MMT modified GFRP composites.
2. Experimental section
2.1. Materials
Isophthalic unsaturated polyester resin (HS-2100) and vinyl ester resins (HS-4430) were supplied by Changzhou Huake Resin Co. Ltd (China). Bidirectional (0 °/90 °) E-glass plain woven fabrics (800 g m−2) were collected from Sinoma Nanjing Fiberglass Research & Design Institute (China). The organo-montmorillonite (OMMT) was supplied by Zhejiang Fenghong New Materials Co. Ltd (China). The OMMT is an organosilicate where the surface of the OMMT was modified with octadecylamine and vinyltrimethoxysilane. ZnO (max. particle size 45 micron) was purchased from Sigma-Aldrich. All chemicals were used as received, without further purification.
2.2. Preparation of ZnO/OMMT filled GFRP nanocomposites
The ZnO and OMMT were dried in an oven for 9 h at 90 °C. The appropriate amount of ZnO and OMMT were dispersed into UP resin or vinyl ester VE resin. The ZnO concentration in the resin was 0, 1, 2, 3, and 4 wt%, and the OMMT concentration in the resin was 0, 4, 3, 2, and 1 wt%, respectively. The ZnO/OMMT/UP or ZnO/OMMT/VE mixture was mixed with a mechanical mixer for 30 min for each group. ZnO/OMMT filled GFRP nanocomposites, consisting of bidirectional () E-glass woven fabrics with ZnO/OMMT/UP or ZnO/OMMT/VE mixture, were made by manual lay-up process. Methyl ethyl ketone peroxide (MEKP) and cobalt naphthenate were added as a curing agent and an accelerator, respectively. The effect of ratios of curing agent and accelerator on the properties of the composite are shown in Supplementary Information, figure S1 is available online at stacks.iop.org/MRX/7/035301/mmedia. According to the experimental results, the best ratios of curing agent and accelerator were chosen as 1 wt% of MEKP and 0.1 wt% of cobalt naphthenate. All the specimens were cured at 20 ± 5 °C. The specimens were cut in the dimensions of 200 mm × 15 mm × 7 mm and 40 mm × 15 mm × 7 mm for the flexural test and shear test based on ASTM D7264/D7264M-15 [31] and ASTM D2344 [32], respectively.
2.3. Accelerated UV weathering
The composite specimens were exposed to fluorescent UV light in an accelerated weathering chamber. The specimens were exposed to UV for 90 days at 50 °C. The exposure section remained dry. The specimens were illuminated by UVA-340 fluorescent lamps (wavelength ≈340 nm) with a radiation level of 0.8 W m−2.
2.4. Hygrothermal aging
To study the effect of hygrothermal aging on the properties of nanocomposites, specimens were aged in hygrothermal environment chamber with different temperature values, including 30 °C, 50 °C and 60 °C, and the relative humidity was at 95%.
2.5. Weight loss
The weight of the specimens under accelerated UV weathering condition were measured at regular intervals to study their weight loss behavior. At least five specimens were tested for each group. The weight loss of the specimens was calculated by the equation (1):

where
are the measured weight of the specimen before and after the exposure of UV radiation, respectively.
2.6. Color characterization
Apparent color change is considered to be a significant sign of composite properties, especially after exposure to sunlight and ultraviolet light [30]. The NS810 spectrophotometer manufactured by Shenzhen Threenh Technology Co., Ltd was used to collect the surface lightness and color data of the specimen exposed to accelerated UV weathering condition according to ASTM D7856 [33]. In this test, L* refers to the measurement of lightness, while a* and b* give the color components in the green-red and blue-yellow range, respectively.
2.7. Absorption tests
Water absorption measurements were performed according to ASTM D5229 [34]. The data of specimens were recorded periodically after exposed to hygrothermal aging condition. At regular time intervals, the samples were taken out, wiped to remove surface moisture, and then weighed to monitor the moisture absorption. At least five specimens were tested for each group. The moisture absorption (Mt) was calculated using the equation (2).

where mi is the initial mass of the specimen, and mt is the mass of the specimen at exposure time t.
2.8. Mechanical tests
After each exposure period, the mechanical tests of the specimens were carried out, including flexural test and short-beam-shear test. A WDW-50E universal testing machine with 50 kN capacity was used. Five specimens were tested for each group. Flexural properties of specimens were measured based on ASTM D7264/D7264M-15 [31]. A supported span-to-depth ratio of 16:1 was maintained for all tested specimens. The dimensions of the flexural specimens were 200 mm × 15 mm × 7 mm and the span length was set at 140 mm. Before applying the load, the appropriate load equipment was installed and the machine calibrated. The specimens were loaded at a loading rate of 2 mm min−1.
The short-beam-shear test is a widely used method for characterizing the inter-laminar failure resistance of FRP composites. This test method involves loading a beam under three-point bending with the special dimensions such that an inter-laminar shear failure is induced. The apparent inter-laminar shear strength can be measured from this method [35]. Short-beam-shear test were conducted according to standard ASTM D2344 [32]. The dimensions of the short-beam-shear specimens were 40 mm × 15 mm × 7 mm. The mechanical testing speed was set at 2 mm min−1.
3. Results and discussion
3.1. Effect of ZnO and OMMT concentrations
The content of ZnO and OMMT in the ZnO/OMMT filled VE-based GFRP nanocomposites plays an important role in their properties. Flexural tests and shear tests of specimens manufactured with different content of ZnO and OMMT were performed to evaluate the optimum proportion. Specimens with 1 wt% OMMT and 4 wt% ZnO showed better flexural strength and shear strength than those of other specimens (table 1). Thus, specimens with 1 wt% OMMT and 4 wt% ZnO were chosen to conduct the following tests.
Table 1. Flexural strength and shear strength of VE-based GFRP with different content of OMMT and ZnO
No. | OMMT content (wt%) | ZnO content (wt%) | Flexural strength (MPa) | Shear strength (MPa) |
---|---|---|---|---|
M0Z0 | 0 | 0 | 377.55 | 23.22 |
M1Z4 | 1 | 4 | 457.63 | 28.63 |
M2Z3 | 2 | 3 | 414.09 | 25.03 |
M3Z2 | 3 | 2 | 408.88 | 24.42 |
M4Z1 | 4 | 1 | 403.46 | 24.32 |
3.1.1. Weight loss of specimens under UV radiation condition
Figure 1 shows the effects of exposure time on the mass change of the specimens under UV radiation and hygrothermal conditions, respectively. Under UV radiation condition, the data increased with time for all specimens including UP-based GFRP, VE-based GFRP, nano modified UP-based GFRP, and nano modified VE-based GFRP. After 90 days of exposure to UV radiation, the mass loss of VE-based GFRP, UP-based GFRP, nano modified VE-based GFRP, and nano modified VE-based GFRP were 0.76%, 1.10%, 0.50% and 0.54%, respectively. The results indicated that the mass loss of VE-based GFRP was smaller than that of UP-based GFRP, which was consistent with the results reported in the previous literatures [36]. The mass loss of specimens can be attributed to the dissociation of C–C and C–H bonds and the break of polymer chains caused by UV light energy [37, 38]. In addition, it can be seen that the addition of nanoparticles reduced the mass loss of unsaturated-based GFRP and VE-based GFRP.
Figure 1. Weight loss versus square root of time for the specimens exposed to UV radiation condition.
Download figure:
Standard image High-resolution image3.2. Surface color variations of specimens under UV radiation condition
Figure 2(a) presents lightness (L*) of the specimens under ultraviolet radiation condition. The 90-day aging of UP-based GFRP and VE-based GFRP under UV radiation condition produced a lightness increase more than 16.5% and 22.0%, respectively. Compared with UP-based GFRP and VE-based GFRP, L* value of nano modified UP-based GFRP and VE-based GFRP increased by 14.2% and 8.2%, respectively. Measurements of the color variation in the green-red-range (a*) and blue-yellow range (b*) are detailed in figures 2(b) and (c), respectively. After 90 days aging, the a* value of UP-based GFRP and VE-based GFRP decreased by 31.7% and 68.5%, respectively. Whereas, the decrease of a* value was only 18.4% and 13.6% for nano modified UP-based GFRP and VE-based GFRP, respectively. The results indicated that there was a slight degradation of the green part of the color and a tendency to red for the specimens after 90 days aging. In the meantime, on the blue-yellow scale, the 90-day aging generated 7.7 units and 6.2 units of increment of the yellow component for UP-based GFRP and VE-based GFRP, respectively. Compared with UP-based GFRP and VE-based GFRP, the b* value of nano modified UP-based GFRP and VE-based GFRP increased 3.2 units and 1.51 units, respectively. The results indicated that after 90 days aging, the color of specimens turned into yellow, which might be caused by photo oxidation. It was noted that the addition of nano particles played a role of keep the stableness in the lightness and color variation for specimens exposed to UV radiation condition.
Figure 2. (a) Lightness (L*), color variation in the (b) green-red-range (a*) and (c) blue-yellow-range (b*) of the specimens exposed to UV radiation condition with different time.
Download figure:
Standard image High-resolution image3.3. Moisture absorption of specimens under hygrothermal condition
After 90-day aging in hygrothermal condition, the average moisture uptake curves of specimens are presented in figure 3. Each data point represents the average value obtained from five replicated specimens. In line with the moisture diffusion theory, Mt was plotted versus the square root of time to show the initial linear diffusion curve. For the initial part of the curves, moisture uptakes of specimens increased linearly with the square root of time, and then increased slowly followed by leveling off moisture absorption, which appeared to follow the classic Fick's law [39]. At exposure time of 90 days, the moisture absorption values of UP-based GFRP, VE-based GFRP, nano modified UP-based GFRP, nano modified VE-based GFRP exposed to hygrothermal condition at 30 °C were 0.15%, 0.12%, 0.11%, and 0.09%, respectively. The results indicated that the moisture absorption values of UP-based GFRP and nano modified UP-based GFRP were more than those of VE-based GFRP and nano modified VE-based GFRP, which was ascribed to the lower water permeability of the VE resins respect to UP resins. Also, the increase of temperature accelerated the level of moisture absorption, which was consistent with results reported by Xian [40].
Figure 3. Moisture absorption versus square root of time for the specimens exposed to hygrothermal condition at different temperatures: (a) 30 °C; (b) 50 °C and (c) 60 °C.
Download figure:
Standard image High-resolution imageTo calculate the diffusion coefficient from data of specimens in hygrothermal aging on moisture absorption as a function of time, Fickian theory equation was used [41]. For the process of one-dimensional, unsteady diffusion was governed by

where c is the concentration of the diffusing species, t is the conditioning time, x is the position in the diffusing direction, and D is the diffusion coefficient or diffusivity. When an object absorbed moisture in the air, the following boundary conditions were adopted:


where c0 is the initial moisture content, is the equilibrium moisture content, h is the thickness of the specimens, and F is the introduced proportional constant. Hence, Mtcan be expressed as follow:

where
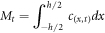


At the initial stages of moisture absorption, the solution for Fick's law at small times reduced to

This equation indicated that the initial stage of moisture absorption was linearly related to square root of time and was a fixed value. Then, equation (7) can be expressed as

where k is a constant.
The value of Mt of nano modified VE-based GFRP at temperature of 30 °C, 50 °C and 60 °C under hygrothermal condition and the fitting expression was expressed as equations (9)–(11).



According to the table 2, the theoretical values were nearly consistent with the experimental values. However, in the actual test, after a period of hygrothermal aging, the specimen gradually reached saturation and the water absorption rate slowed down, so the theoretical values were slightly larger than the experimental values.
Table 2. Comparison of results of theoretical value and experiment values for moisture uptake
30 °C | 50 °C | 60 °C | |
---|---|---|---|
Aging time (days) | Theoretical value(Experiment value) (%) | ||
0 | 0(0) | 0(0) | 0(0) |
15 | 0.03(0.023) | 0.471(0.384) | 0.408(0.378) |
30 | 0.041(0.045) | 0.667(0.68) | 0.759(0.669) |
45 | 0.077(0.078) | 0.817(0.85) | 1.052(0.902) |
60 | 0.088(0.083) | 0.943(0.961) | 1.215(1.039) |
75 | 0.092(0.085) | 1.054(0.981) | 1.258(1.160) |
90 | 0.103(0.095) | 1.155(0.975) | 1.288(1.187) |
3.4. Mechanical tests
The changes in the flexural strength of UP-based GFRP, VE-based GFRP, nano modified UP-based GFRP, nano modified VE-based GFRP exposed to UV radiation condition versus time are shown in figure 4. A two-phase evolution of the flexural strength was observed. First, a consolidation phase showed an increase in the flexural strength for all GFRP composites. During this stage, the flexural strength of composites improved slightly due to the action of post-curing reaction [42]. As shown in figure 4, the flexural strength attained the top retention at 30 days. The strength increased 11.4%, 16.5%, 3.10%, and 8.57% for UP-based GFRP, VE-based GFRP, nano modified UP-based GFRP, nano modified VE-based GFRP exposed to UV radiation condition, respectively. After 30 days radiation, a degradation phase followed, which exhibited a drastic drop of the flexural strength. After 90 days of radiation, the loss of flexural strength was 14.69%, 8.58%, 11.47%, and 6.85% for UP-based GFRP, VE-based GFRP, nano modified UP-based GFRP, nano modified VE-based GFRP exposed to UV radiation condition, respectively. The results indicated that the addition of ZnO and OMMT reduced the loss of strength of specimens.
Figure 4. Flexural strength versus time for the specimens exposed to UV radiation condition.
Download figure:
Standard image High-resolution imageSimilarly, figure 5 shows that the specimens in hygrothermal condition at three temperatures showed different degradation degrees of flexural strength. At immersion time of 90 days, the flexural strength of UP-based GFRP, VE-based GFRP, nano modified UP-based GFRP, nano modified VE-based GFRP exposed to hygrothermal condition at 30 °C decreased by 9.61%, 8.77%, 7.83%, and 7.26%, respectively. The results indicated that the strength loss of UP-based GFRP and nano modified UP-based GFRP were more than those of VE-based GFRP and nano modified VE-based GFRP. Additionally, the increase of temperature accelerated the degradation of flexural strength of specimens. The deteriorations in flexural properties can be attributed to water diffusion, resulting in degradation of resin, fiber fractures, and fiber-matrix debonding [43].
Figure 5. Flexural strength versus time for the specimens exposed to hygrothermal condition at different temperatures: (a) 30 °C; (b) 50 °C; (c) 60 °C.
Download figure:
Standard image High-resolution imageOverall results and variation tendency of short-beam strength for the composites exposed to UV radiation and hygrothermal conditions are shown in figures 6 and 7. The interlaminar shear strength values were slightly increased at the initial phase due to residual post-cure. And the maximum raise was 3.59% and 2.39% at the end of the first 30 days for VE-based GFRP and nano modified VE-based GFRP exposed to UV radiation condition. Then there was a steady decline, followed by a rapid drop over the rest of the exposure period. After 90 days, the loss of the interlaminar shear strength of VE-based GFRP and nano modified VE-based GFRP exposed to UV radiation condition was 14.27% and 11.16%, respectively.
Figure 6. Interlaminar shear strength versus time for the specimens exposed to UV radiation condition.
Download figure:
Standard image High-resolution imageFigure 7. Interlaminar shear strength versus time for the specimens exposed to hygrothermal condition at different temperatures: (a) 30 °C, (b) 50 °C and (c) 60 °C.
Download figure:
Standard image High-resolution imageAt immersion time of 90 days, the interlaminar shear strength of VE-based GFRP and nano modified VE-based GFRP exposed to hygrothermal condition at 30 °C decreased by 15.45% and 10.78%, respectively. However, the increase of temperature had little effect on the degradation of interlaminar strength of specimens. This could be attributed to the changes in interlaminar strength depended only on interfacial mechanisms without substantial physical/mechanical degradation of the matrix.
3.5. Morphology analysis
To determine whether UV radiation or hygrothermal condition caused any physical damage to VE-based GFRP composites and nano modified VE-based GFRP composites, the specimen surface microstructure was examined by SEM. Typical images of the control specimens are presented in figures 8(a) and 9(a). No evidence of degradation was observed on the glass fiber and fiber/matrix interface when VE-based GFRP specimens and nano modified VE-based GFRP specimens aged at 0 day. Additionally, the polymer started to deteriorate and more and more gaps observed between fiber and resin as the UV radiation exposure time increased. It was possible to observe that debonding occurred between fiber and resin, and consequent fiber pullout for VE-based GFRP specimens exposed to UV radiation after 90 days, as shown in figure 8(b). This was definitely a main reason why the flexural properties and interlaminar shear properties degraded. It was noted that the degradation of nano modified VE-based GFRP was less than that of VE-based GFRP, as shown in figures 8(b) and 9(b). The SEM results were consistent with the flexural test results, which indicated that the flexural strength retention of the VE-based GFRP and nano modified VE-based GFRP exposed to UV radiation after 90 days were roughly 91% and 94%, respectively.
Figure 8. SEM micrographs of VE-based GFRP composite surfaces exposed to UV radiation condition at (a) 0 day, (b) 90 days.
Download figure:
Standard image High-resolution imageFigure 9. SEM micrographs of nano modified VE-based GFRP composite surfaces exposed to UV radiation condition at (a) 0 day, (b) 90 days.
Download figure:
Standard image High-resolution imageThe adhesion behavior between the fiber and the matrix plays an important role in the loading transfer from the matrix to the fiber. SEM micrographs of VE-based GFRP composite and nano modified VE-based GFRP composite surfaces exposed to hygrothermal condition at different temperatures are shown in figures 10 and 11. The micrographs in figures 10(a)–(c) show the surfaces of the aged specimens exposed to hygrothermal condition for 90 days at 30 °C, 50 °C, and 60 °C, respectively. As we expect, the fiber breakage as well as fiber pull-out and a higher degree of polymeric deterioration occurred due to the increase in temperature [12, 15]. For specimens exposed to hygrothermal condition at 60 °C with 90 days, figure 10(c) shows that serious debonding occurs between the fiber and matrix and consequent fiber pull-out. In the case of temperature, it was obvious that resin hydrolysis and debonding at the interface were the major reasons for the degradation of flexural properties and shear properties for GFRP composites. It was also noted that the degradation of nano modified VE-based GFRP was less than that of VE-based GFRP, as shown in figures 11(a)–(c). The SEM results were consistent with the flexural and shear test results.
Figure 10. SEM micrographs of VE-based GFRP composite surfaces exposed to hygrothermal condition at different temperatures: (a) 30 °C, (b) 50 °C, and (c) 60 °C.
Download figure:
Standard image High-resolution imageFigure 11. SEM micrographs of nano modified VE-based GFRP composite surfaces exposed to hygrothermal condition at different temperatures: (a) 30 °C, (b) 50 °C, and (c) 60 °C.
Download figure:
Standard image High-resolution image3.6. Long-term durability prediction
According to the Arrhenius rate model, a commonly used life prediction model in accelerated aging testing, the Arrhenius type relationship formulation [41, 44] is expressed by equation (12):

where L(T) represents the quantifiable measure of life, T is the temperature in Kelvin, C and B are the model parameters to be determined. Invert both sides of equation (12) to get equation (13):

Equation (13) represents a straight line in the slope-intercept form, where B is the slope of the line, ln(C) is the intercept and the variable on the horizontal axis is the inverse of temperature. The equation (13) can be written as equation (14):

The experimental percent retention of ultimate flexural strength can be calculated by equation (15):

where T and RT are temperatures in degree Celsius.
The flexural strength retention of nano modified VE-based GFRP of each time was plotted (figure 12). Table 3 shows the predicted ultimate flexural strength retention along with the experiment data and error as per equation (16).

Figure 12. Fitting curves of flexural strength.
Download figure:
Standard image High-resolution imageTable 3. Predicted and experimental ultimate flexural strength retention for nano modified VE-based GFRP under hygrothermal condition.
30 °C | 50 °C | 60 °C | ||||
---|---|---|---|---|---|---|
Aging duration (days) | Predicted (Expt.) | Error (%) | Predicted (Expt.) | Error (%) | Predicted (Expt.) | Error (%) |
30 | 100(100) | 0 % | 100(100) | 0 % | 100(100) | 0 % |
60 | 95.12(95.58) | −0.48% | 92.88(94.3) | −1.51% | 91.86(92.1) | −0.26% |
90 | 92.17(91.87) | 0.3% | 88.64(88.91) | −0.3% | 87.04(86.88) | 0.18% |
120 | 90.07 | — | 85.64 | — | 83.63 | — |
150 | 88.45 | — | 83.31 | — | 80.97 | — |
180 | 87.12 | — | 81.41 | — | 78.81 | — |
365 | 81.96 | — | 74.02 | — | 70.4 | — |
730 | 76.81 | — | 66.78 | — | 62.17 | — |
1825 | 70.2 | — | 57.18 | — | 51.26 | — |
3650 | 65.15 | — | 49.93 | — | 43.01 | — |
By the same method, the life prediction equation of shear strength of nano modified VE-based GFRP. Additionally, the life prediction equation of flexural strength and shear strength of VE-based GFRP are shown in tables 4 and 5, respectively. According to the prediction, after 10 years, the flexural strength retention of nano modified VE-based GFRP under hygrothermal condition at 30 °C, 50 °C, and 60 °C will be 65.15%, 49.93%, and 43.01%, respectively. The corresponding shear strength retention will be 64.36%, 47.98%, and 40.53% respectively. The 10 years prediction of flexural strength retention of VE-based GFRP are 8.92%, 2.62% and −0.25% respectively, and the shear strength retention will be 44.24%, 24.75%, and 15.89% respectively. The results indicated that the flexural strength and shear strength of nano modified GFRP were much higher than those of unmodified GFRP after ten years.
Table 4. Relationship between ultimate flexural strength retention and time for VE-based GFRP under hygrothermal condition.
Aging duration (days) | Relationship between percent retention and 1/T | Aging duration (days) | Relationship between percent retention and 1/T |
---|---|---|---|
30 |
![]() |
180 |
![]() |
60 |
![]() |
365 |
![]() |
90 |
![]() |
730 |
![]() |
120 |
![]() |
1825 |
![]() |
150 |
![]() |
3650 |
![]() |
Table 5. Relationship between shear strength retention and time for VE-based GFRP under hygrothermal condition
Aging duration (days) | Relationship between percent retention and 1/T | Aging duration (days) | Relationship between percent retention and 1/T |
---|---|---|---|
30 |
![]() |
180 |
![]() |
60 |
![]() |
365 |
![]() |
90 |
![]() |
730 |
![]() |
120 |
![]() |
1825 |
![]() |
150 |
![]() |
3650 |
![]() |
4. Conclusions
This paper presents the durability of ZnO/OMMT filled GFRP composites under UV radiation and hygrothermal (30 °C, 50 °C and 60 °C and 95% relative humidity) conditions. The study focused on the effects of the addition of ZnO/OMMT nanoparticles on mechanical properties such as flexural properties and interlaminar shear strength. Based on the above study, the main findings of this study are summarized as follows:
- The mass loss of all specimens including UP-based GFRP, VE-based GFRP, nano modified UP-based GFRP, and nano modified VE-based GFRP increased with time under UV radiation condition. The mass loss of VE-based GFRP was less than that of UP-based GFRP because of the difference of functional groups between UP resin and VE resin. Additionally, the addition of ZnO/OMMT nanoparticles reduced the mass loss of UP-based GFRP and VE-based GFRP under UV radiation condition.
- The moisture absorption of UP-based GFRP, VE-based GFRP, nano modified UP-based GFRP, and nano modified VE-based GFRP increased nonlinearly as the temperature rose. Elevating the temperature increased the moisture absorption capacity and diffusion coefficient of all the specimens in hygrothermal condition. The equilibrium moisture absorption of nano modified UP-based GFRP and nano modified VE was less than that of UP-based GFRP and VE-based GFRP because of the effect of nano particles on preventing the diffusion of water molecules into matrix.
- After 90 days of UV radiation, compared with VE-based GFRP, the flexural strength and interlaminar shear strength increased by 23.5% and 27.8% for nano modified VE-based GFRP. Additionally, after 90 days of aging in hygrothermal at 30 °C, 50 °C, and 60 °C, with the addition of nano particle for VE-based GFRP, the flexural strength enhanced 23.2%, 25.7%, and 26.5%, respectively, and the interlaminar shear strength increased 30.1%, 27.0%, and 27.2%, respectively. The flexural and shear test results were consistent with SEM results. It was noted that the degradation of nano modified VE-based GFRP was less than that of VE-based GFRP.
- An analytical model was proposed to predict the long term durability of the unmodified GFRP and nano modified GFRP in hygrothermal condition. The analytical results matched well with the experimental results. According to the prediction, the flexural strength and shear strength of nano modified GFRP were much higher than those of unmodified GFRP after ten years.
Acknowledgments
The authors gratefully acknowledge the financial support received from the National Natural Science Foundation of China (grant number 51778285).