Improving the Flame Retardancy of Bamboo Slices by Coating With Melamine–Phytate via Layer-by-Layer Assembly
- 1School of Engineering, Zhejiang A&F University, Hangzhou, China
- 2ZhongHang Monitoring & Testing Technology Research Institute Co., Ltd, Hangzhou, China
- 3Zhejiang Provincial Collaborative Innovation Center for Bamboo Resources and High-Efficiency Utilization, Hangzhou, China
Bamboo is a rich natural resource in the Asia Pacific, and it is widely used in the construction and decoration industry. Meanwhile, bamboo is an extremely combustible natural polymer material. Herein, the bamboo slices were treated with melamine and phytic acid using layer-by-layer (LBL) assembly technology to improve their flame retardancy properties. The morphology and chemical composition of untreated and treated bamboo slices were measured by scanning electron microscopy equipped with energy dispersive X-ray analysis and Fourier transform infrared spectra. The results showed that two-dimensional melamine–phytate (MP) nanoflakes were successfully formed and deposited on the bamboo surface. The deposition of the MP coating caused the earlier degradation of the bamboo to form char, according to thermogravimetric analysis. The peak heat release rates of the treated bamboo slices were reduced by more than 28% compared to those of the untreated ones. The MP coating promoted the formation of thermally stable char, which was responsible for the significant improvement in flame retardancy. Besides, the char layer with excellent thermal resistance performed a vital role in suppressing flame spread.
Introduction
Bamboo is a natural polymer material and a rich natural resource in the Asia-Pacific region (Sharma et al., 2015a). As it has the advantages of fast growth, high yield, and excellent mechanical properties, bamboo has been widely used in the production of bamboo-based composites, for example, laminated bamboo board, bamboo plywood, bamboo particleboard, and bamboo scrimber (Verma and Chariar, 2012; Yu et al., 2017a; Zhang et al., 2019). In addition, due to its characteristic appearance, bamboo has been used as a decorative material for buildings (Hu et al., 2012). However, bamboo’s flammability results in a potential fire hazard when used in the indoor environment. Therefore, it is crucial for enhancing bamboo’s flame retardancy.
Many efforts have been devoted to improving the flame retardancy of bamboo. Traditional methods to improve the flame retardancy of bamboo materials included impregnation (Guo et al., 2019), copolymerization (Bidsorkhi et al., 2017), and surface coating (Yao et al., 2019). Although the impregnation method has the advantages of low cost and applicability, it needs to use high-voltage equipment. Copolymerization is generally used for the flame retardancy of acrylic fiber and polyester (Manfredi et al., 2006). Despite the fact that this composite has substantial flame-retardant properties, its processing is time-consuming and costly. Surface coating is directly brushing flame retardant onto materials’ surface, which is a simple process that effectively improves the flame retardancy of materials (Yang et al., 2019). However, the painting process is easy to cause pollution and endanger the health of operators.
Traditional fire-retarding methods are prompted by the development of new technology, such as surface grafting (Fei et al., 2017), sol–gel methods (Grancaric et al., 2017), and layer-by-layer self-assembly (Teng et al., 2019). In recent years, LBL assembly technology, which is primarily based on the alternating electrostatic attraction of oppositely charged polyelectrolytes, has been used to endow bamboo with flame retardancy (Carosio et al., 2017; Wang et al., 2018a). Compared with traditional flame-retardant methods, the LBL assembly technique can minimize the risk of environmental pollution. Simultaneously, the LBL assembly technique is easy to operate under mild conditions (e.g., room temperature and using water as solvent), and the immersion solution can be recycled (Li et al., 2011). Therefore, the LBL assembly technology is superior to the traditional methods because it has the advantages of simplicity, operability, versatility, and controllability of thickness at the nanoscale level.
Furthermore, the choice of flame retardant is also particularly important for improving the flame-retardant properties of bamboo. Traditional flame retardants are usually abandoned due to their toxicity and less efficiency (Sharma et al., 2015b; He et al., 2020). The natural macromolecules become the promising and sustainable flame retardant for fiber materials, such as chitosan (Xiong et al., 2019), phytic acid (PA) (Cheng et al., 2016; Liu et al., 2021), tannic acid (Nam et al., 2017; Yang et al., 2018), and protein-based biomacromolecules (Malucelli et al., 2014). For plant-derived PA, it has been used as a novel flame-retardant agent due to its inartificial and phosphorus-rich features; the ability of phosphate groups to ionically react with positively charged molecules has the premise of being a polyanionic candidate to develop the flame-retardant coatings through the LBL assembly technique (Yu et al., 2017b; Cheng et al., 2019).
As a critical N-rich organic base, melamine has multiple amino groups and π–π stacking capacity (Huang et al., 2012), and PA is an organic acid that is safe for the environment (Fang et al., 2018; Wang et al., 2018b). Hence, in this work, the cationic melamine and anionic PA were synthesized into flame-retardant melamine–phytate (MP) and deposited on bamboo slices by the LBL assembly technique. The distribution of MP on the surface of the bamboo was observed. Besides, the thermal stability and flame-retardant performances of the treated bamboo slices were investigated. The residue char was investigated as well as the flame-retardant mechanism.
Experimental Section
Materials
Bamboo slices were provided by Zhejiang ZEN Bamboo Co., Ltd. (Hangzhou, China). Melamine (C3H6N6, ≥95%), phytic acid (C6H18O24P6, 50 wt%), and acetic acid (CH3COOH, AR, ≥99%) were purchased from Aladdin Biochemical Reagent Co., Ltd. (Shanghai, China). The water used was deionized. All chemicals and solvents were used without further purification.
Flame-Retardant Treatment of Bamboo Slices by LBL Assembly
An anionic polyelectrolyte solution containing 1.5 wt% phytic acid was prepared, and a cationic polyelectrolyte solution containing 3.0 wt% melamine was obtained by changing the pH value of the solution to four using acetic acid. At room temperature, the melamine and PA solutions were vigorously mixed until the polyelectrolyte was fully dissolved. The oven-dried bamboo slices were first dipped in the melamine solution for 5 min, rinsed with deionized water to eliminate any remaining polyelectrolytes, and air-dried at room temperature. Subsequently, the bamboo slices were dipped into the PA solution for 5 min, rinsed with deionized water, and then dried at 40, 60, and 80°C for 30 min and finally at 103°C. The process was repeated, and Figure 1A shows the diagrammatic representation of this technique. For comparison, the bamboo samples treated with melamine and PA by LBL assembly were marked as B/MP-BL, and one circle was denoted as one bilayer (BL).
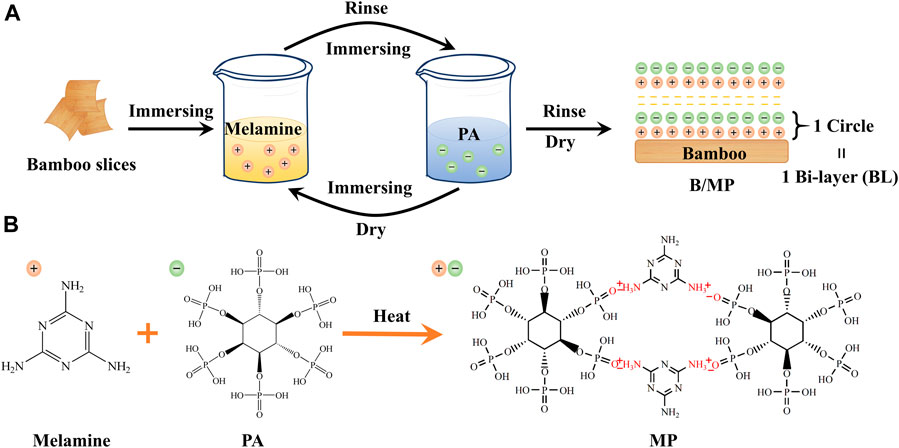
FIGURE 1. Diagrammatic illustration of LBL treatment of bamboo slices (A) and the synthetic route of MP (B).
The weight gain percent (WPG) of the treated bamboo samples was calculated according to the following formula: WPG (%) = (M2−M1)/M1, where M1 is the oven-dry weight of bamboo samples before treatment and M2 is the oven-dry weight after treatment.
Characterization
Attenuated total reflection Fourier transform infrared (ATR-FTIR, Nicolet iN10, Thermo Science, United States) was used to build the ATR-FTIR spectra of untreated and treated bamboo with a wavenumber range of 4,000–400 cm−1 and a resolution of 4 cm−1. The morphology of untreated and treated bamboo and the residue char after combustion test samples were investigated using a scanning electron microscope (Quanta FEG250, FEI, United States) at an acceleration voltage of 20.0 kV. The elemental distribution on the treated bamboo samples’ surface was also observed using energy dispersive X-ray (EDX). The samples were subjected to thermogravimetric analysis (TGA) on a thermal analyzer (Q5000, TA Instruments, United States) in a N2 and air atmosphere at a rate of 20 °C/min from 30 to 800°C. The limiting oxygen index (LOI) was evaluated using an oxygen index instrument (JF-5, Nanjing Jiangning Ltd., China).
The samples’ combustion tests were performed by a cone calorimetry test (CCT) (FTT0007, Fire Testing Technology Ltd., United Kingdom) according to the ISO 5660-1 procedure. Each sample (dimensions of 100 × 100 × 5 mm3) was made up by combining bamboo slices with a small amount of urea–formaldehyde resin glue, and then the samples were exposed to an irradiance of 50 kW m−2. For each treatment, the test was repeated four times.
Results and Discussion
A one-step finishing process was carried out for flame-retardant bamboo slices; electrostatic absorption was used to deposit positively charged melamine and negatively charged PA on bamboo surfaces using the LBL assembly process (Figure 1A). Here, we illustrate the formation mechanism of melamine–phytate (MP) via melamine and PA self-assembly (Figure 1B). The MP was synthesized by ionic attraction and π–π stacking self-assembly interactions. Melamine with amino groups can form aggregates when it interacts with acidic sites in PA. Each molecular structure of PA has six phosphate groups that can interact with six melamine molecules. The MP was formed by ionic attractions between MP and π–π stacking self-assembly of triazine in melamine (Shang et al., 2019).
WPG and ATR-FTIR Analysis
The bamboo slices obtained a linear increase in WPG by increasing the number of cycles (Figure 2A), and the WPG of the bamboo slices reached 3.9% after five cycles. It showed that the content of chemicals on the surface of the bamboo increased with the treatment times. To understand the loaded compounds’ chemical composition, ATR-FTIR spectra were obtained to detect the characteristic groups on the bamboo surface. As shown in Figure 2B, the peaks at 3,470 and 3,330 cm−1 are assigned to typical NH2 in melamine (Lv et al., 2005). These peaks seem to have disappeared in the spectrum of B/MP-5BL, which is due to the formation of -NH3 +O- in MP (Shang et al., 2019). The bands at approximately 1,649 cm−1 are attributed to O-P-O stretching vibration for phytic acid (Jiang et al., 2012). A peak at 1,056 cm−1 for the stretching vibration of C-O-C was observed in the spectrum of untreated bamboo, indicating the existence of cellulose in bamboo (Sun et al., 2015). Additionally, the absorbance ratios (O-P-O/C-O-C: A1649/A1056 cm−1) of B/MP-5BL are higher than those of the untreated one, indicating that phytic acid has been deposited on the bamboo surface successively (Liu et al., 2018). As a result, this evidence indicated that MP is obtained and successfully loaded on the bamboo surface via LBL assembly of melamine and PA.
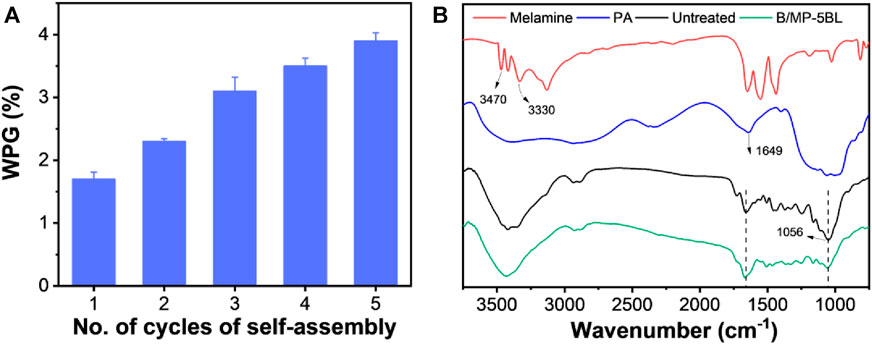
FIGURE 2. WPG of treated bamboo with different numbers of assembling cycles (A) and ATR-FTIR of untreated and treated bamboo (B).
Morphology of the Treated Bamboo
Figure 3 shows the SEM images of the surface of treated and untreated bamboo slices. There are no additional substances observed on the surface of the untreated bamboo (Figure 3A). For the treated bamboo, the MP complex attached to the bamboo surface irregularly, and the formation of the microsphere was deposited in the cell lumen (Figure 3B). Furthermore, the morphology of MP is a two-dimensional sheet-like structure after LBL assembly of melamine with PA (Figure 3C). It is attributed to the ionic attraction and π–π stacking self-assembly (Shang et al., 2019). Two-dimensional nanomaterials are well known for their ability as flame retardants as they can delay gas diffusion and heat transfer (Sun et al., 2019). The elemental composition of treated bamboo after five cycles is shown in Figure 3D. The P and N elements were clearly detected in the treated bamboo, in addition to the C and O elements possessed by bamboo. It was also confirmed that MP accumulated on the bamboo’s surface.
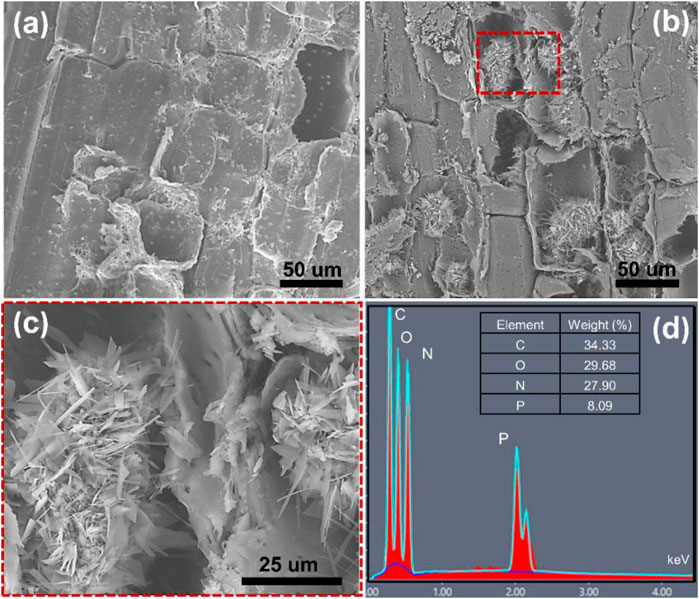
FIGURE 3. SEM image of untreated bamboo (A), treated bamboo after five cycles (B, C), and EDX patterns of treated bamboo (D).
Thermal Analysis of the Treated Bamboo
The effect of MP on the thermal stability of bamboo slices was systematically investigated under nitrogen and air atmospheres, respectively. TG under the nitrogen atmosphere is used to simulate the combustion behavior under the surface of the combustion material. The thermal degradation of the untreated bamboo can be divided into two stages (Figure 4A). The thermal degradation of main components of the untreated bamboo in different temperature ranges is as follows: 200–260°C for hemicellulose, 240–350°C for cellulose, and 280–500°C for lignin (Yao et al., 2019). The treated bamboo exhibited the same two stages of thermal deterioration as the untreated bamboo. For the treated bamboo, the initial temperature of decomposition is lower than untreated samples. The thermal decomposition of MP possibly caused this phenomenon. This phosphorus- and nitrogen-containing species showed a lower thermal stability than the matrix, which could decompose in advance to form char to protect the matrix (Zhang et al., 2014). As predicted, the char yield increased as the number of MP coating cycles increased. The thermal decomposition of PA produced acid species, which promoted the formation of char from bamboo with plentiful hydroxyl groups. This process could protect the underlying matrix because it is beneficial for char residue formation (Qu et al., 2017). Furthermore, gas diffusion and heat transfer can be slowed by the two-dimensional structure. Thus, treated bamboo’s thermal stability was improved in the high-temperature range of 400–800°C. Besides, the maximum mass loss rate of treated bamboo was lower than that of untreated bamboo (Figure 4B), which was due to the char inhibiting mass transfer and leading to the prevention of further deterioration of the inner bamboo.
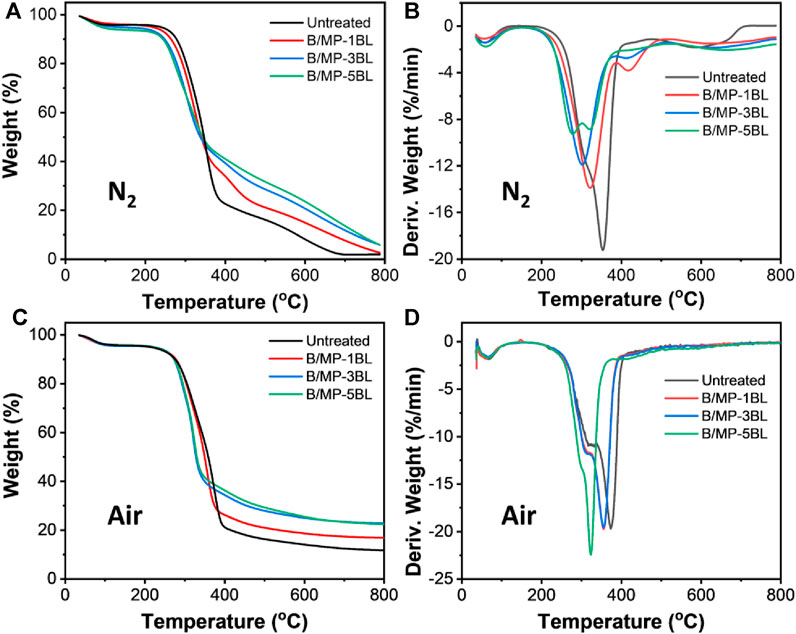
FIGURE 4. TG and DTG profiles of untreated and treated bamboo slices under nitrogen (A, B) and air atmospheres (C, D).
Under the air atmosphere conditions, it was also found from the TG and DTG curves that there were two degradation processes in the untreated and treated bamboo (Figures 4C,D). The degradation process is similar to that in the N2 atmosphere. The final residue of B/MP-5BL was 22.7% (the loading of MP was 3.9%), while the final residue of the untreated bamboo was 11.6%. As a result, the treated bamboo samples obtained a much higher char yield than the untreated one at 800°C. In conclusion, the MP coating is able to favor the generation of thermal resistance char during the degradation of bamboo in a remarkable way, protecting the bamboo against thermal degradation.
Flame-Retardant Property of the Treated Bamboo
The LOI is a common parameter used for assessing the flammability of materials, which refers to the minimum concentration of oxygen in an oxygen–nitrogen mixture. A higher LOI value indicates better flame-retardant capability (Ren et al., 2018). The untreated bamboo has a low LOI value of 21.5% (Figure 5A). After coating the bamboo substrate with MP, the LOI value increases slightly, demonstrating the improvement in its flame-retardant property.
Furthermore, the flame-retardant properties of untreated and treated bamboo were investigated by the cone calorimetry technique. The time to ignition (TTI) of treated bamboo is slightly higher than that of the untreated one (Figure 5B). Untreated bamboo released heat fast upon ignition with a peak heat release rate (HRR) value of 268 kW m−2 (Figure 6A). After deposition of one cycle of MP coating, the peak HRR value of B/MP-1BL was reduced to 191 kW m−2, corresponding to a 28.7% reduction. They were further increasing the cycles of MP coating, which slightly affected the peak HRR values. The decreased HRR value suggested that the combustion process had been suppressed effectively. Moreover, the incorporation of MP reduces the total heat release (THR) values from 33.7 MJ m−2 for untreated bamboo to 23.4 MJ m−2 for B/MP-5BL, which is 30.6% lower than that of untreated bamboo (Figure 6B). It is attributed to the PA, which can be thermally decomposed into pyrophosphate and polyphosphate to promote the formation of char and protect the underlying matrix from burning (Bao et al., 2012). Furthermore, as the number of MP coating treatment cycles increased, the THR of the treated bamboo decreased.
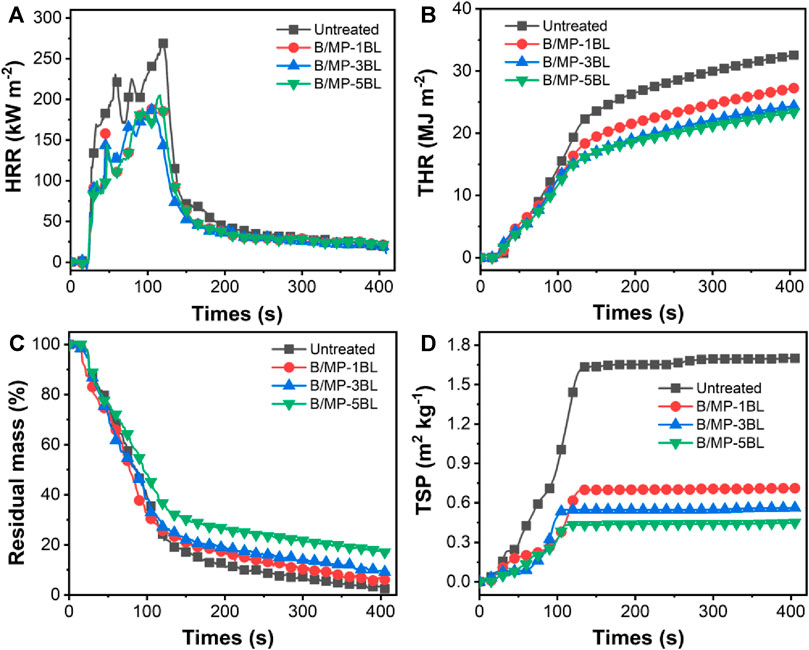
FIGURE 6. Cone calorimetry tests of untreated and treated bamboo with different times of the cycle: HRR (A), THR (B), residual mass (C), and TSP (D).
As shown in Figure 6C, untreated bamboo loses 80% mass in 120°s. Compared to untreated bamboo, treated bamboo shows a slower mass loss rate and a lower mass loss. The combustion of treated bamboo was delayed, that is attributed to the MP promote the generation of charresidues (Shang et al., 2019). The total smoke production (TSP) of the untreated bamboo rapidly reached maximum due to fast combustion (Figure 6D). The B/MP-1BL exhibited a noticeable reduction (58.8%) and a slight delay in the TSP. With the increase of processing cycles, the treated bamboo–produced smoke was further decreased. The TSP was reduced by 67.1 and 73.5% at B/MP-3BL and B/MP-5BL, respectively, compared to the untreated bamboo.
Morphology of Char Residues
When the untreated bamboo substrate was ignited, it burned rapidly and almost entirely, leaving a residue of an insufficient char layer when it was cooled. Moreover, the cells were exfoliated and separated for untreated bamboo char due to the poor flame and heat resistance of natural bamboo (Figure 7A). By contrast, cells in the B/MP-5BL maintained the same shape and size as before burning (Figure 7B). Besides, the MP residues were found on the surface of the treated bamboo char residues. The char can resist heat and mass transfer even further, slowing the bamboo’s thermal decomposition and protecting it from being burned further. Besides, the thermal decomposition of MP produced H2O and NH3, which dilute oxygen and slow combustion. It made MP act as a mass transfer barrier and had a particular protective effect on the bamboo substrate.
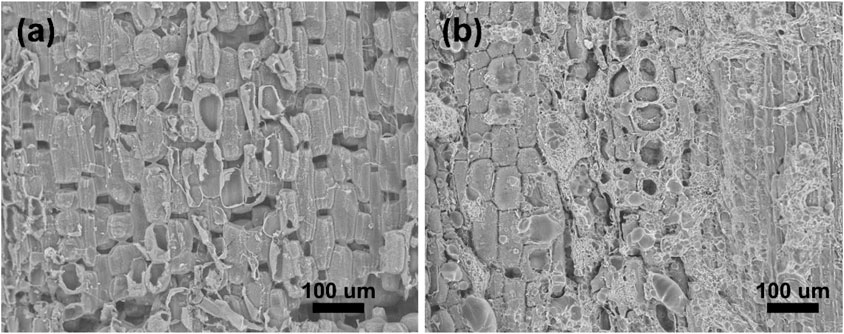
FIGURE 7. SEM micrographs of untreated bamboo (A) and B/MP-5BL (B) char residues after cone calorimetry tests.
Conclusion
This work has shown that melamine and phytic acid made into melamine–phytate (MP) for improving the flame-retardant performance of bamboo slices via LBL assembly technology. The phosphorus- and nitrogen-rich features of the MP made it very effective to protect the bamboo substrates against thermal degradation and combustion. Compared to untreated bamboo, treated bamboo’s peak heat release rate and total heat release were reduced by more than 28 and 30%, respectively. Furthermore, the obviously decreased smoke generation capacity was also achieved. The significant improvement in flame retardancy was attributed to the MP coating which promoted the formation of thermally stable char. Thus, MP deposition on bamboo via LBL assembly technology as a flame retardant requires fewer processing steps and is more industrially applicable. More work is needed to evaluate the environmental stability of the MP-coated bamboo slices.
Data Availability Statement
The raw data supporting the conclusion of this article will be made available by the authors, without undue reservation.
Author Contributions
PL and WC executed the experiment and wrote the manuscript. YY conceived and designed the study and the experiment plan. LM revised the manuscript. JH, YX, and XZ analyzed the experimental results.
Funding
The work was financially supported by the National Natural Science Foundation of China (Grant No. 31800473) and the Natural Science Foundation of Zhejiang province (Grant No. LY17C160007).
Conflict of Interest
PL was employed by the ZhongHang Monitoring & Testing Technology Research Institute Co., Ltd.
The remaining authors declare that the research was conducted in the absence of any commercial or financial relationships that could be construed as a potential conflict of interest.
References
Bao, C., Guo, Y., Yuan, B., Hu, Y., and Song, L. (2012). Functionalized Graphene Oxide for Fire Safety Applications of Polymers: a Combination of Condensed Phase Flame Retardant Strategies. J. Mater. Chem. 22, 23057–23063. doi:10.1039/C2JM35001G
Bidsorkhi, H. C., Adelnia, H., Naderi, N., Moazeni, N., and Mohamad, Z. (2017). Ethylene Vinyl Acetate Copolymer Nanocomposites Based on (Un)modified Sepiolite: Flame Retardancy, thermal, and Mechanical Properties. Polym. Compos. 38, 1302–1310. doi:10.1002/pc.23695
Carosio, F., Alongi, J., Paravidino, C., and Frache, A. (2017). Improving the Flame Retardant Efficiency of Layer by Layer Coatings Containing Deoxyribonucleic Acid by post-diffusion of Hydrotalcite Nanoparticles. Materials 10, 709. doi:10.3390/ma10070709
Cheng, X.-W., Guan, J.-P., Chen, G., Yang, X.-H., and Tang, R.-C. (2016). Adsorption and Flame Retardant Properties of Bio-Based Phytic Acid on Wool Fabric. Polymers. 8, 122. doi:10.3390/polym8040122
Cheng, X.-W., Tang, R.-C., Yao, F., and Yang, X.-H. (2019). Flame Retardant Coating of Wool Fabric with Phytic Acid/polyethyleneimine Polyelectrolyte Complex. Prog. Org. Coat. 132, 336–342. doi:10.1016/j.porgcoat.2019.04.018
Fang, F., Song, P., Ran, S., Guo, Z., Wang, H., and Fang, Z. (2018). A Facile Way to Prepare Phosphorus-Nitrogen-Functionalized Graphene Oxide for Enhancing the Flame Retardancy of Epoxy Resin. Composites Commun. 10, 97–102. doi:10.1016/j.coco.2018.08.001
Fei, M.-E., Xie, T., Liu, W., Chen, H., and Qiu, R. (2017). Surface Grafting of Bamboo Fibers with 1,2-Epoxy-4-Vinylcyclohexane for Reinforcing Unsaturated Polyester. Cellulose. 24, 5505–5514. doi:10.1007/s10570-017-1497-1
Grancaric, A. M., Colleoni, C., Guido, E., Botteri, L., and Rosace, G. (2017). Thermal Behaviour and Flame Retardancy of Monoethanolamine-Doped Sol-Gel Coatings of Cotton Fabric. Prog. Org. Coat. 103, 174–181. doi:10.1016/j.porgcoat.2016.10.035
Guo, W., Kalali, E. N., Wang, X., Xing, W., Zhang, P., Song, L., et al. (2019). Processing Bulk Natural Bamboo into a strong and Flame-Retardant Composite Material. Ind. Crops Prod. 138, 111478. doi:10.1016/j.indcrop.2019.111478
He, W., Song, P., Yu, B., Fang, Z., and Wang, H. (2020). Flame Retardant Polymeric Nanocomposites through the Combination of Nanomaterials and Conventional Flame Retardants. Prog. Mater. Sci. 114, 100687. doi:10.1016/j.pmatsci.2020.100687
Hu, N., Li, X. J., Wu, Y. Q., Li, X. G., and Xue, Z. C. (2012). Preliminary Research on Manufacturing Technology of Thin Bamboo Veneer Consolidated Composite Floor. Amr. 503-504, 74–77. doi:10.4028/www.scientific.net/amr.503-504.74
Huang, S. T., Wang, G. L., Li, N. B., and Luo, H. Q. (2012). Mechanism of the pH-Induced Aggregation Reaction between Melamine and Phosphate. RSC Adv. 2, 10948–10954. doi:10.1039/c2ra21415f
Jiang, G., Qiao, J., and Hong, F. (2012). Application of Phosphoric Acid and Phytic Acid-Doped Bacterial Cellulose as Novel Proton-Conducting Membranes to PEMFC. Int. J. Hydrogen Energ. 37, 9182–9192. doi:10.1016/j.ijhydene.2012.02.195
Li, Y.-C., Mannen, S., Morgan, A. B., Chang, S., Yang, Y.-H., Condon, B., et al. (2011). Intumescent All-Polymer Multilayer Nanocoating Capable of Extinguishing Flame on Fabric. Adv. Mater. 23, 3926–3931. doi:10.1002/adma.201101871
Liu, C., Zhang, T., Luo, Y., Wang, Y., Li, J., Ye, T., et al. (2021). Multifunctional Polyurethane Sponge Coatings with Excellent Flame Retardant, Antibacterial, Compressible, and Recyclable Properties. Composites B: Eng. 215, 108785. doi:10.1016/j.compositesb.2021.108785
Liu, L., Huang, Z., Pan, Y., Wang, X., Song, L., and Hu, Y. (2018). Finishing of Cotton Fabrics by Multi-Layered Coatings to Improve Their Flame Retardancy and Water Repellency. Cellulose. 25, 4791–4803. doi:10.1007/s10570-018-1866-4
Lv, P., Wang, Z., Hu, K., and Fan, W. (2005). Flammability and thermal Degradation of Flame Retarded Polypropylene Composites Containing Melamine Phosphate and Pentaerythritol Derivatives. Polym. Degrad. Stab. 90, 523–534. doi:10.1016/j.polymdegradstab.2005.04.003
Malucelli, G., Bosco, F., Alongi, J., Carosio, F., Di, Blasio, A., Mollea, C., et al. (2014). Biomacromolecules as Novel green Flame Retardant Systems for Textiles: an Overview. RSC Adv. 4, 46024–46039. doi:10.1039/C4RA06771A
Manfredi, L. B., Rodríguez, E. S., Wladyka-Przybylak, M., and Vázquez, A. (2006). Thermal Degradation and Fire Resistance of Unsaturated Polyester, Modified Acrylic Resins and Their Composites with Natural Fibres. Polym. Degrad. Stab. 91, 255–261. doi:10.1016/j.polymdegradstab.2005.05.003
Nam, S., Condon, B. D., Xia, Z., Nagarajan, R., Hinchliffe, D. J., and Madison, C. A. (2017). Intumescent Flame-Retardant Cotton Produced by Tannic Acid and Sodium Hydroxide. J. Anal. Appl. Pyrolysis. 126, 239–246. doi:10.1016/j.jaap.2017.06.003
Qu, T., Yang, N., Hou, J., Li, G., Yao, Y., Zhang, Q., et al. (2017). Flame Retarding Epoxy Composites with Poly(phosphazene-Co-Bisphenol A)-coated boron Nitride to Improve thermal Conductivity and thermal Stability. RSC Adv. 7, 6140–6151. doi:10.1039/C6RA27062J
Ren, D., Li, J., Xu, J., Wu, Z., Bao, Y., Li, N., et al. (2018). Efficient Antifungal and Flame-Retardant Properties of ZnO-TiO2-Layered Double-Nanostructures Coated on Bamboo Substrate. Coatings. 8, 341. doi:10.3390/coatings8100341
Shang, S., Yuan, B., Sun, Y., Chen, G., Huang, C., Yu, B., et al. (2019). Facile Preparation of Layered Melamine-Phytate Flame Retardant via Supramolecular Self-Assembly Technology. J. Colloid Interf. Sci. 553, 364–371. doi:10.1016/j.jcis.2019.06.015
Sharma, B., Gatóo, A., Bock, M., and Ramage, M. (2015a). Engineered Bamboo for Structural Applications. Construction Building Mater. 81, 66–73. doi:10.1016/j.conbuildmat.2015.01.077
Sharma, N. K., Verma, C. S., Chariar, V. M., and Prasad, R. (2015b). Eco-friendly Flame-Retardant Treatments for Cellulosic green Building Materials. Indoor Built Environ. 24, 422–432. doi:10.1177/1420326X13516655
Sun, B., Huang, A., Wang, Y., and Liu, J. (2015). Natural Bamboo (Neosinocalamus affinisKeng) Fiber Identification Using FT-IR and 2D-IR Correlation Spectroscopy. J. Nat. Fibers. 12, 1–11. doi:10.1080/15440478.2013.796907
Sun, Y., Yuan, B., Chen, X., Li, K., Wang, L., Yun, Y., et al. (2019). Suppression of Methane/air Explosion by Kaolinite-Based Multi-Component Inhibitor. Powder Techn. 343, 279–286. doi:10.1016/j.powtec.2018.11.026
Teng, Z., Ye, C., Zheng, C., Chen, F., Li, Y., Wen, S., et al. (2019). Layer-by-layer Self-Assembly of Ce-Doped Titanate Nanotube-Based Hybrid Coating on Bamboo Fibre Materials for Flame Retardancy and Thermostability. Polym. Degrad. Stab. 168, 108950. doi:10.1016/j.polymdegradstab.2019.108950
Verma, C. S., and Chariar, V. M. (2012). Development of Layered Laminate Bamboo Composite and Their Mechanical Properties. Composites Part B: Eng. 43, 1063–1069. doi:10.1016/j.compositesb.2011.11.065
Wang, J., Sun, Q., Sun, F., Zhang, Q., and Jin, C. (2018a). Layer-by-layer Self-Assembly of Reduced Graphene Oxide on Bamboo Timber Surface with Improved Decay Resistance. Eur. J. Wood Prod. 76, 1223–1231. doi:10.1007/s00107-018-1295-y
Wang, J., Zhan, J., Mu, X., Jin, X., Chu, F., Kan, Y., et al. (2018b). Manganese Phytate Dotted Polyaniline Shell Enwrapped Carbon Nanotube: Towards the Reinforcements in Fire Safety and Mechanical Property of Polymer. J. Colloid Interf. Sci. 529, 345–356. doi:10.1016/j.jcis.2018.06.038
Xiong, Z., Zhang, Y., Du, X., Song, P., and Fang, Z. (2019). Green and Scalable Fabrication of Core-Shell Biobased Flame Retardants for Reducing Flammability of Polylactic Acid. ACS Sustain. Chem. Eng. 7 (9), 8954–8963. doi:10.1021/acssuschemeng.9b01016
Yang, H., Yu, B., Song, P., Maluk, C., and Wang, H. (2019). Surface-coating Engineering for Flame Retardant Flexible Polyurethane Foams: A Critical Review. Composites Part B: Eng. 176, 107185. doi:10.1016/j.compositesb.2019.107185
Yang, T.-T., Guan, J.-P., Tang, R.-C., and Chen, G. (2018). Condensed Tannin from Dioscorea Cirrhosa Tuber as an Eco-Friendly and Durable Flame Retardant for Silk Textile. Ind. Crops Prod. 115, 16–25. doi:10.1016/j.indcrop.2018.02.018
Yao, X., Du, C., Hua, Y., Zhang, J., Peng, R., Huang, Q., et al. (2019). Flame-retardant and Smoke Suppression Properties of Nano MgAl-LDH Coating on Bamboo Prepared by an In Situ Reaction. J. Nanomater. 2019, 1–12. doi:10.1155/2019/9067510
Yu, X., Pan, Y., Wang, D., Yuan, B., Song, L., and Hu, Y. (2017a). Fabrication and Properties of Biobased Layer-By-Layer Coated Ramie Fabric-Reinforced Unsaturated Polyester Resin Composites. Ind. Eng. Chem. Res. 56, 4758–4767. doi:10.1021/acs.iecr.7b00101
Yu, Y., Liu, R., Huang, Y., Meng, F., and Yu, W. (2017b). Preparation, Physical, Mechanical, and Interfacial Morphological Properties of Engineered Bamboo Scrimber. Construction Building Mater. 157, 1032–1039. doi:10.1016/j.conbuildmat.2017.09.185
Zhang, T., Yan, H., Shen, L., Fang, Z., Zhang, X., Wang, J., et al. (2014). A Phosphorus-, Nitrogen- and Carbon-Containing Polyelectrolyte Complex: Preparation, Characterization and its Flame Retardant Performance on Polypropylene. RSC Adv. 4, 48285–48292. doi:10.1039/C4RA09243K
Keywords: bamboo, melamine, phytic acid, LBL, thermal stability, flame retardant
Citation: Lin P, Xu Y, Hou J, Zhang X, Ma L, Che W and Yu Y (2021) Improving the Flame Retardancy of Bamboo Slices by Coating With Melamine–Phytate via Layer-by-Layer Assembly. Front. Mater. 8:690603. doi: 10.3389/fmats.2021.690603
Received: 03 April 2021; Accepted: 12 May 2021;
Published: 04 June 2021.
Edited by:
Pingan Song, University of Southern Queensland, AustraliaReviewed by:
Bihe Yuan, Wuhan University of Technology, ChinaXuejun Lai, South China University of Technology, China
Miaojun Xu, Northeast Forestry University, China
Copyright © 2021 Lin, Xu, Hou, Zhang, Ma, Che and Yu. This is an open-access article distributed under the terms of the Creative Commons Attribution License (CC BY). The use, distribution or reproduction in other forums is permitted, provided the original author(s) and the copyright owner(s) are credited and that the original publication in this journal is cited, in accordance with accepted academic practice. No use, distribution or reproduction is permitted which does not comply with these terms.
*Correspondence: Wenbo Che, chewenbo@zafu.edu.cn; Youming Yu, yuyouming@zafu.edu.cn