Humidity-Sensing Material Cottonid – Microstructural Tuning for Improved Actuation and Fatigue Performance
- 1Department of Materials Test Engineering (WPT), TU Dortmund University, Dortmund, Germany
- 2Biogenic Polymers, TUM Campus Straubing (TUMCS), Technical University of Munich, Munich, Germany
Adaptive actuators are stimuli-responsive materials able to make a direct use of primary energy to produce motion, as it is well known from motile plant structures. Changes in environmental conditions, such as temperature and humidity, trigger passive movements without the need of metabolism or the use of electrical energy. This bioinspired adaptive mechanism is an alternative and sustainable approach in terms of energy conservation in technical applications. The cellulose-based functional material Cottonid is a promising candidate in this context. It is hygroscopic and possesses a process-related structural anisotropy, which results in direction-dependent actuation and fatigue performance. Since Cottonid is a modified natural material, its microstructure is tunable through chemical modification of the cellulose during the manufacturing process. To assess the influence of varying manufacturing parameters on the microstructure, the actuation behavior as well as the mechanical properties, a parameter study was carried out to identify the most promising modifications for stimuli-responsive element production while maintaining mechanical robustness. This was accomplished with respect to variations of the cellulose source, the chemical catalyst for cellulose modification, temperature of the catalyst bath Tcat as well as reaction time treact. Specimens’ microstructures were investigated with scanning electron microscopy, infrared spectroscopy as well as X-ray diffraction. The actuation behavior was characterized over instrumented experiments in a climate chamber in varying environmental conditions, whereas the environmental fatigue behavior was evaluated in tests with superimposed medial and mechanical loading. Obtained results identified Tcat as most influential process parameter onto resulting material actuation properties, which enables a limitation of the possible process window. The findings are used to develop tailored functional materials, where anisotropy and hygroscopicity can be adjusted through the manufacturing process.
Introduction
Active adaptation to changing environmental conditions as an intrinsic material function is a biological mechanism that is increasingly used as an energy-efficient approach in the development of technical systems. A large proportion of plants react to external stimuli, such as varying temperature and relative humidity of the environment or solar radiation, with adaptive behavior expressed by passive or active movements (Markin et al., 2008; Forterre, 2013). Depending on the weather conditions, these movements serve, e.g., for seed dispersal or protection, to catch prey (in carnivorous plants) or for defense. The direction of the resulting movements is determined either by the microstructural structure of the cell walls (passive) or by the position of the acting stimulus (active). A vivid example of moisture-driven passive movements is the pinecone, which opens its scales for reproduction in a dry environment and closes them at high humidity to protect the seed. The reason for the bending movement of the scales lies in their bilayered structure, whereas the layers have a divergent orientation of the cellulose fibrils, which results in differently pronounced swelling and shrinking behavior (Fratzl and Barth, 2009; Reyssat and Mahadevan, 2009; van Opdenbosch et al., 2016).
In current research, this efficient relationship between structure and function of a material is implemented in many ways in bio-based or artificial material systems. The transfer and targeted use of the structural properties of biological systems is fundamental, whereby the pine cone is a frequently used model as a bilayered actuator. Stimulus-adaptive material systems can offer advantages in a wide variety of technical applications. Based on thermo-, hygro-, or light-sensitive materials, such sensor/actuator systems can directly convert primary energy, such as solar radiation or hydropower, into a technically usable kinetic energy, which is energetically advantageous (Dai et al., 2013; Guiducci et al., 2016; Shin et al., 2018).
In addition to saving energy, the use of renewable resources in material development is also an important aspect. Cellulose-based material systems are hygroscopic and an efficient raw material basis for humditiy-responsive actuators. With wood as a traditional construction material, the moisture-controlled swelling and shrinkage behavior is exploited, for example, in the manufacture of curved architectural elements. Through the intelligent combination of layers with varying microstructural composition, complex geometries are developed by treatment with moisture, which are used, among other things, in the form of facade elements. As smart building skins, they adapt their position and orientation to the ambient conditions as required and provide shade in the event of high solar energy irradiation without permanently obstructing the view (Menges, 2012; Grönquist et al., 2018).
In this context, Cottonid is a functional material based on chemically modified cellulose, which shows a pronounced and directed swelling and shrinking behavior in reaction to varying relative humidity. It is manufactured over the parchmentizing process, which is a chemical process used to modify organic polymers, like native cellulose, changing its molecular structure. The chemical catalyst partly dissolves the polymer chains, whereas the degree of dissolution is highly dependent on the source of the cellulose as well as the process conditions (Vieweg and Becker, 1965; Jedvert and Heinze, 2017). As cellulosic raw material, unsized filter paper is used, based on cotton linters, wood pulp or a mixture of the two. The paper is fed into a tempered catalyst bath, comprising a zinc chloride (ZnCl2) solution or a sulfuric acid (H2SO4) solution, where the surfaces of the cellulose fibrils are etched superficially and new intra- and intermolecular hydrogen bonds can form in one and between several paper layers. This results in a chemical modification of the native cellulose (cellulose 1) in the raw paper. The amount of paper layers fed into the process defines the thickness of the end product. This provides a simple and energy-efficient procedure to manufacture thin and flexible Cottonid for actuators or thicker, dimensionally stable material for construction purposes. After the catalyst bath, Cottonid is washed out until no chemical residuals are left and subsequently dried and planned. Due to the directed paper making process, the cellulose short fibers have a preferred direction, which can be seen in the anisotropic material behavior of Cottonid. The highest mechanical strength can be detected in manufacturing direction and is comparable to common technical plastics, like PA or PVC. Perpendicular to manufacturing direction, a pronounced swelling and shrinking behavior in reaction to humidity is present (Mittendorf, 2016; Scholz et al., 2016, 2019b; Esch, 2018).
Cottonid was already patented in the late 19th century but was replaced later by synthetic plastics in most technical applications. Today, with regard to sustainability and eco-friendliness, Cottonid is a resource-efficient alternative again (Taylor, 1871; Scholz et al., 2019a). Further, the motivation for investigations on this material lies in the fact, that in contrast to wood it is possible to influence and tune the microstructure of Cottonid by specifically adjusting the manufacturing parameters. Delignified cellulose bulk materials e.g., are also wood-derived and structure and properties are highly dependent on the heterogeneity of the wood substrate (Rüggeberg and Burgert, 2015; Frey et al., 2018; Scholz et al., 2019b). Since structural directionality is a beneficial attribute in terms of mechanical as well as – besides hygroscopicity – swelling properties, Cottonid is an efficient candidate for adaptive humidity-driven actuators. A targeted combination of different Cottonid variants would provide an efficient way of producing architectural components with complex adaptive deformation behavior. To determine the influence of individual process parameters, four different Cottonid variants were investigated in this study with regard to their microstructure and actuation performance. Further, to assess the influence of the process-related predefined orientation of the cellulose fibrils, specimens for fatigue experiments were prepared with different locations in respect to manufacturing direction of the Cottonid sheet.
In this study, the influence of a variation of Tcat and treact on the actuation and fatigue properties of Cottonid is focused taking into account the process-related anisotropic behavior as well as the hygroscopicity of Cottonid.
Experimental Procedure
Sample Preparation
The raw paper for the produced Cottonid variants was obtained from Hahnemühle FineArt GmbH (Dassel, Germany) and has a weight of 320 g/m2 with a material thickness tmat = 0.9 mm. It consists of 100% cotton linters, this raw material basis is subsequently marked as “M.” A 70 wt-% ZnCl2 solution, hereinafter referred to as “Z,” is used as the chemical catalyst for parchmentizing.
In order to determine the influence of the temperature of the catalyst bath Tcat as well as the reaction time treact on the resulting material properties, one paper layer was parchmentized at Tcat,I = 20°C and one at Tcat,II = 50°C with respective reaction times of treact,I = 10 s and treact,II = 60 s. The term catalyst bath is defined as a 70 wt-% ZnCl2 solution in which the chemical modification of the native cellulose in the paper layers takes place. The investigation of interdependencies between a variation of the temperature of this bath (Tcat) and the time a paper layer is placed in it (treact) was focused in this study. The sample designation of the resulting Cottonid variants consists out of the chosen manufacturing parameters (see Table 1). After the chemical reaction, the catalyst residues are washed out again. This is first accomplished in washing baths with decreasing ZnCl2 concentration, starting at 30% by weight and ending at 5% by weight. Finally, it is washed out with pure water until a chloride detection with silver nitrate no longer shows any precipitation. The samples are then smoothed and dried in a calander (Sumet, Denklingen, Germany) under pressure and temperature. In order to prevent a dimensional change of the material due to water absorption from the environment, the samples are stored under-weight in a dry atmosphere until further analysis.
For actuation tests, bilayered Cottonid/paper actuators were prepared, whereas the Cottonid variants represent the hygroscopically active layer and the untreated office paper (area weight 80 g/m2) the passive one. The layers were adhesively bonded with water resistant wood glue D4 (Leimwerk, Nuremberg, Germany). Specimens’ dimensions were 15.0 × 30.0 × 0.5 mm3. To get a first impression on the influence of the manufacturing parameters on the humidity-driven actuation behavior of Cottonid, one specimen was tested for each variant.
For mechanical testing, specimen geometry was chosen according to DIN EN ISO 527. The investigations were carried out on industrial material (“Hornex,” Ernst Krüger GmbH & Co., KG, Geldern, Germany) with a material thickness of tmat = 4.5 mm. Hornex is also parchmentized using a ZnCl2 solution. Specimens were manufactured in 0°, 45°, and 90° according to manufacturing direction of the Cottonid sheet (Scholz et al., 2016, 2019b). Figure 1C displayes Cottonid specimens for mechanical tests and in Figure 1D test setup for fatigue experiments with integrated climate chamber is shown. During fatigue investigations, 16 specimens were tested in sum, i.e., three samples for each varied parameter.
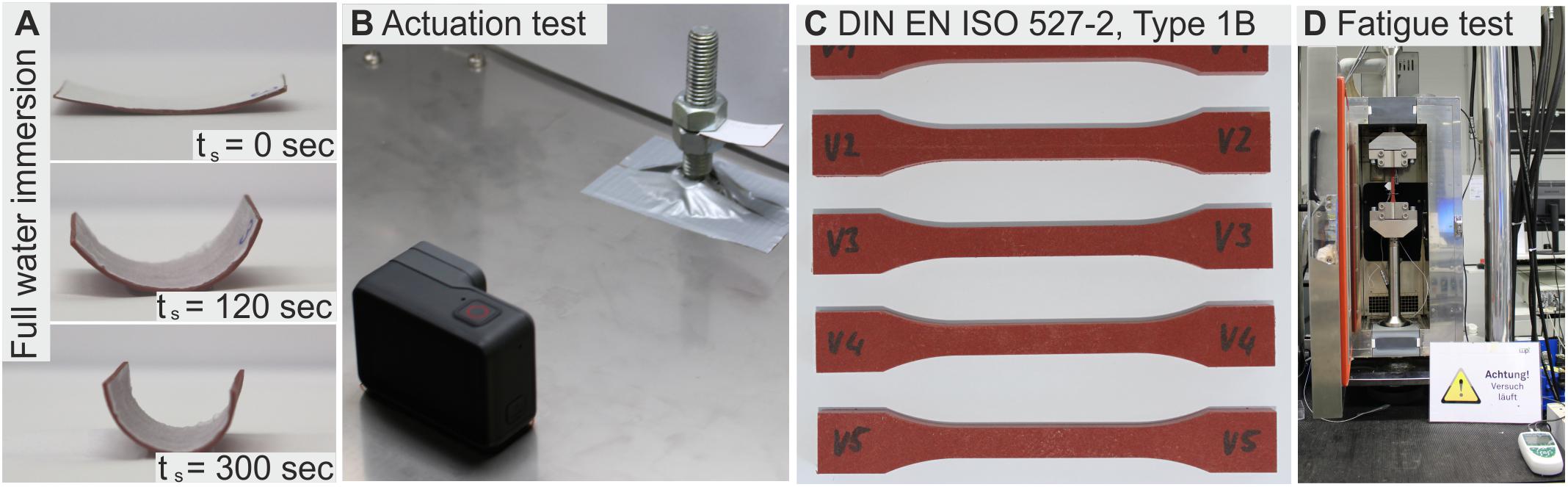
Figure 1. (A) Full water immersion of Cottonid/paper bilayer actuator, (B) Optical monitoring of actuation performance, (C) Cottonid specimens for fatigue testing, (D) Test set up for fatigue testing.
Microstructural Investigations and Analytics
Scanning electron microscopy (SEM) and infrared (IR) spectroscopy are applied to the raw paper “M” and to the manufactured variants M10Z20, M60Z20, M10Z50, and M60Z50 to visualize structural changes in the raw paper caused by the action of the ZnCl2 solution and a variation of Tcat during manufacturing of Cottonid.
The microstructure images were obtained with an FE-REM (MIRA3, Tescan GmbH, Dortmund, Germany) and provide optical information on the reaction degree of the cellulose fibrils as a function of Tcat and treact. Surfaces of the raw paper and Cottonid variants were sputtered with a conductive medium. The absorption of IR radiation is an energy absorption of the material, which, depending on its chemical composition, results in a material-specific spectrum with peaks at characteristic frequencies f or wavelengths ṽ. A Nicolet 380 spectrometer (Thermo Scientific Inc., Waltham, MA, United States) with an ATR module in attenuated total reflection was used for the measurements. In contrast to transmission, this method enables a surface analysis of opaque substances and thus allows a correlation of the information about microstructural changes on the surface obtained by SEM images with the associated chemical processes. The focus lies on the evaluation of the influences of the process parameters Tcat and treact. For the wave number interval from 3,600 to 400 cm–1, 32 scans per sample with a resolution of 4 cm–1 were performed and averaged using the corresponding software (Omnic 7.4.127 Thermo Electron Corp.). A background scan was performed prior to each measurement to avoid overlay of sample material and ambient air. The ratio of crystallinity was determined by the following equitation:
With A1430 is the absorbance ratio at 1,430 cm–1 and A893 is the absorbance ration at 893 cm–1 (Ciolacu et al., 2011).
X-ray diffractograms were collected on a Rigaku Miniflex 600. The diffracted intensity of CuKα radiation (λ = 0.154 nm, 40 kV and 15 mA) was measured in a 2θ range between 5° and 40°, with scan steps 0.02° at 10°/60 s. The crystallinity of the samples was analyzed by using the method of Segal et al. (1951). This method estimates a crystallinity index, which is defined as:
Where I002 is the maximum intensity (in a.u.) of the 002 plane diffraction for cellulose Iα at ∼22°. Iam is the intensity of the amorphous background at 2θ = 18°. Since this is an empirical method for the determination of crystallinity, the values are not absolute, but they indicate the crystallinity change for the Cottonid samples (Bertran and Dale, 1986).
Investigations on Humidity-Driven Actuation Behavior
Investigations on the actuation performance of the different Cottonid variants M10Z20, M60Z20, M10Z50, and M60Z50 were carried out in an alternating climate chamber (MKF 115, Binder, Tuttlingen, Germany). The bilayered Cottonid/paper actuators were clamped at one side and deflection angle Δα was measured on the free end by optical monitoring of a tracking point. Within the test duration, i.e., swelling time of ts = 6 h, several hygroscopic loading cycles between φmax = 95% r.H. and φmin = 40% r.H. were performed, where adsorption and desorption phases were ∼30 min. Ambient temperature was held constant at Tamb = 23°C. In Figure 1A a Cottonid/paper actuator in different swelling states when fully immersed in water and in Figure 1B an extract of the test setup is presented.
Investigations on Fatigue Performance
For the investigation of microstructural and environmental influences on the fatigue behavior of Cottonid, multiple step tests (MST) where performed, which represent a time- and energy-efficient methodology to evaluate and compare the fatigue performance of various materials (Colombo et al., 2012, 2018; Schmiedt-Kalenborn et al., 2019). The detection of physical measured variables during a cyclic mechanical loading provides the basis for characterization of initiation and development of microstructural damage within the specimen before final failure. The test methodology is a resource-efficient alternative for the conventional creation of a SN experimental curve (Walther, 2014).
In this study, MST were performed to evaluate the influence of different specimen locations according to manufacturing direction, meaning investigation of anisotropic deformation behavior, and ambient atmospheres on the fatigue behavior of Cottonid. Tests were performed on a servo hydraulic testing machine (Fmax = 30 kN, Shimadzu, Duisburg, Germany) equipped with an integrable climate chamber (THC, Shimadzu, Duisburg, Germany) to control the surrounding atmosphere. The cyclic loading was applied with a frequency of f = 5 Hz and a sinusoidal load-time function. Stress ratio was R = 0.1, so tension-tension loading was present. Maximum stress at start was σmax,start = 15 MPa and was increased stepwise with Δσmax = 2.5 MPa every ΔN = 104 cycles until failure of the specimen. To detect material’s reactions during loading, specimens were instrumented with thermocouples and deformations were detected contact free via digital image correlation (DIC, Limess Messtechnik & Software GmbH, Krefeld, Germany). For that, a speckle pattern is applied on specimens’ surfaces, which can be monitored by a camera system. MST were performed at two different humidity levels (φlow = 20% r.H., φhigh = 95% r.H.), whereas ambient temperature was held constant at Tamb = 23°C.
Results
Microstructure
Figure 2 displays scanning electron microscopy (SEM) micrographs of the Cottonid variants (Figure 2A) M10Z20, (Figure 2B) M60Z20, (Figure 2C) M10Z50, and (Figure 2D) M60Z50. From left to right, microstructural changes on Cottonid’s surface caused by an increase of the reaction time about Δtreact = 50 s and from top to bottom, changes caused by an increase of the process temperature about ΔTcat = 30 K can be seen. In Figure 2A can be discovered for M10Z20, that due to the short reaction time of treact,I = 10 s and the low process temperature of Tcat,I = 20°C the reaction of the cellulose fibrils has already begun at some locations, but in wide areas there are still unconnected fibrils and defects visible. Increased reaction time of treact,II = 60 s in Figure 2B seems to result in less defects on the surface, but in general the surfaces of M10Z20 and M60Z20 are very similar with regard to the modification stadium of the cellulose. In comparison to that, an increased process temperature of Tcat,II = 50°C results in a stronger reaction of the cellulose fibrils. In Figure 2C only a few very small defects are visible and the fibrils seem to be interconnected over the whole area. The combination of treact,II = 60 s and Tcat,II = 50°C results in the strongest reaction. The fibrils are thicker and shorter in comparison to the other Cottonid variants, are interconnected over the whole area and almost no defects are visible. In general, during the process the fibrils are just superficially etched, so that the original fibrous structure of the paper is still visible. This is reflected in the direction-dependent deformation behavior of Cottonid (Scholz et al., 2016, 2019b). The small white crystals on and in between the fibers are remaining zinc chloride.
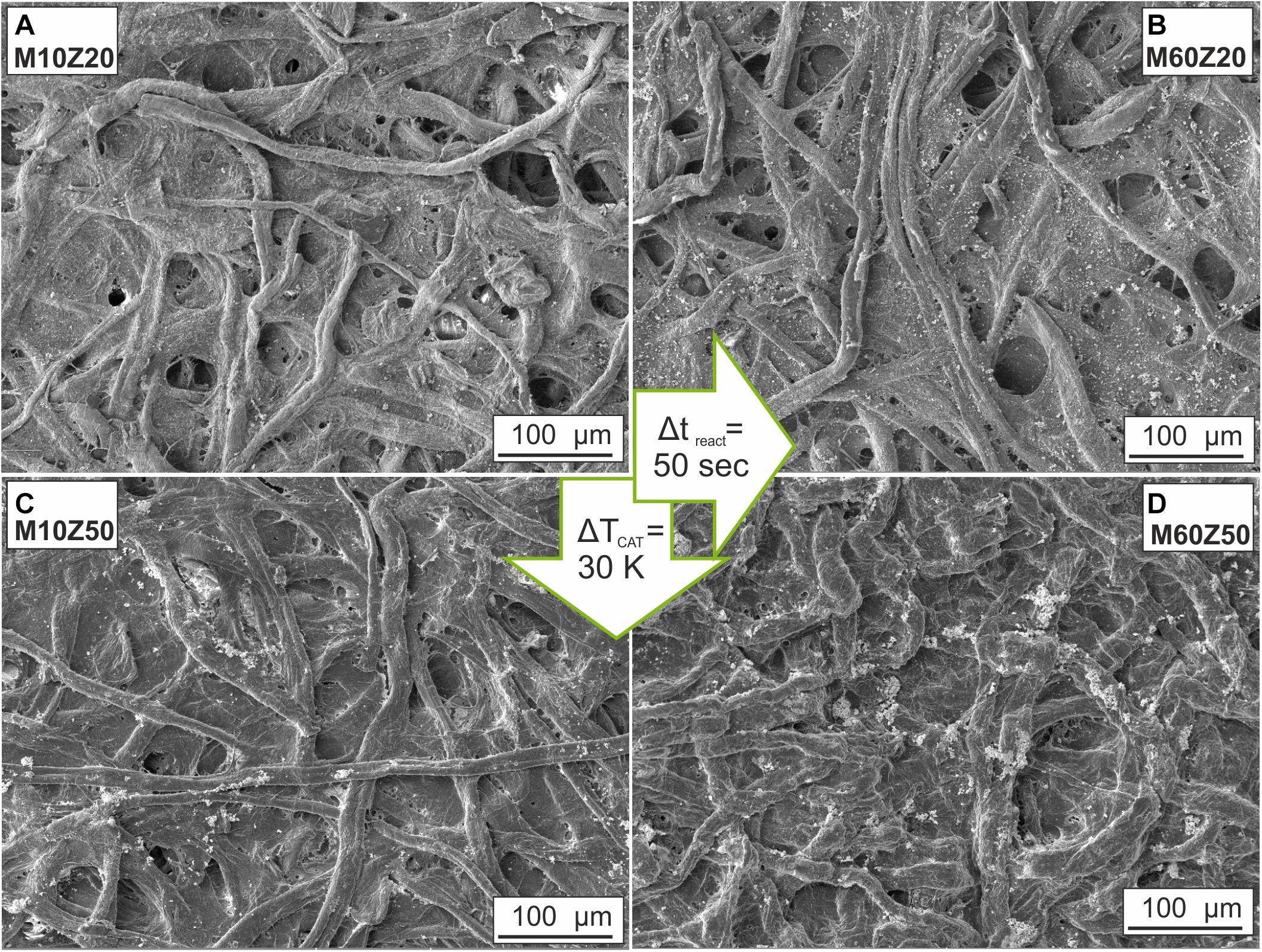
Figure 2. SEM micrographs of different Cottonid variants: (A) M10Z20, (B) M60Z20, (C) M10Z50 and (D) M60Z50.
Figure 3 shows infrared spectra of the raw paper M in relation to the Cottonid variants (Figure 3A) M10Z20, (Figure 3B) M60Z20, (Figure 3C) M10Z50, and (Figure 3D) M60Z50. The spectra were collected in a wavelength interval between 3,600 and 400 cm–1 and all of them show the characteristic peaks for cellulose. In the interval between 3,600 and 3,100 cm–1 the stretching vibrations of the hydroxyl group [ν(–OH)] of the cellulose chains can be seen. The height and area of the peak therefore provides information about the inter- and intra-molecular hydrogen bonds present in the material. The much lower peak at 2,900 cm–1 stands for the stretching vibrations of the alkyle [ν(–CH)] groups. Absorbed water is the reason for the peak at 1,640 cm–1. In the interval between 1,300 and 900 cm–1 peaks of the alcohols derived from to the cellulose chains can be observed. The peak of the glycosidic linkage, which is also known as amorphous peak, can be found at 898 cm–1 (Ciolacu et al., 2011).
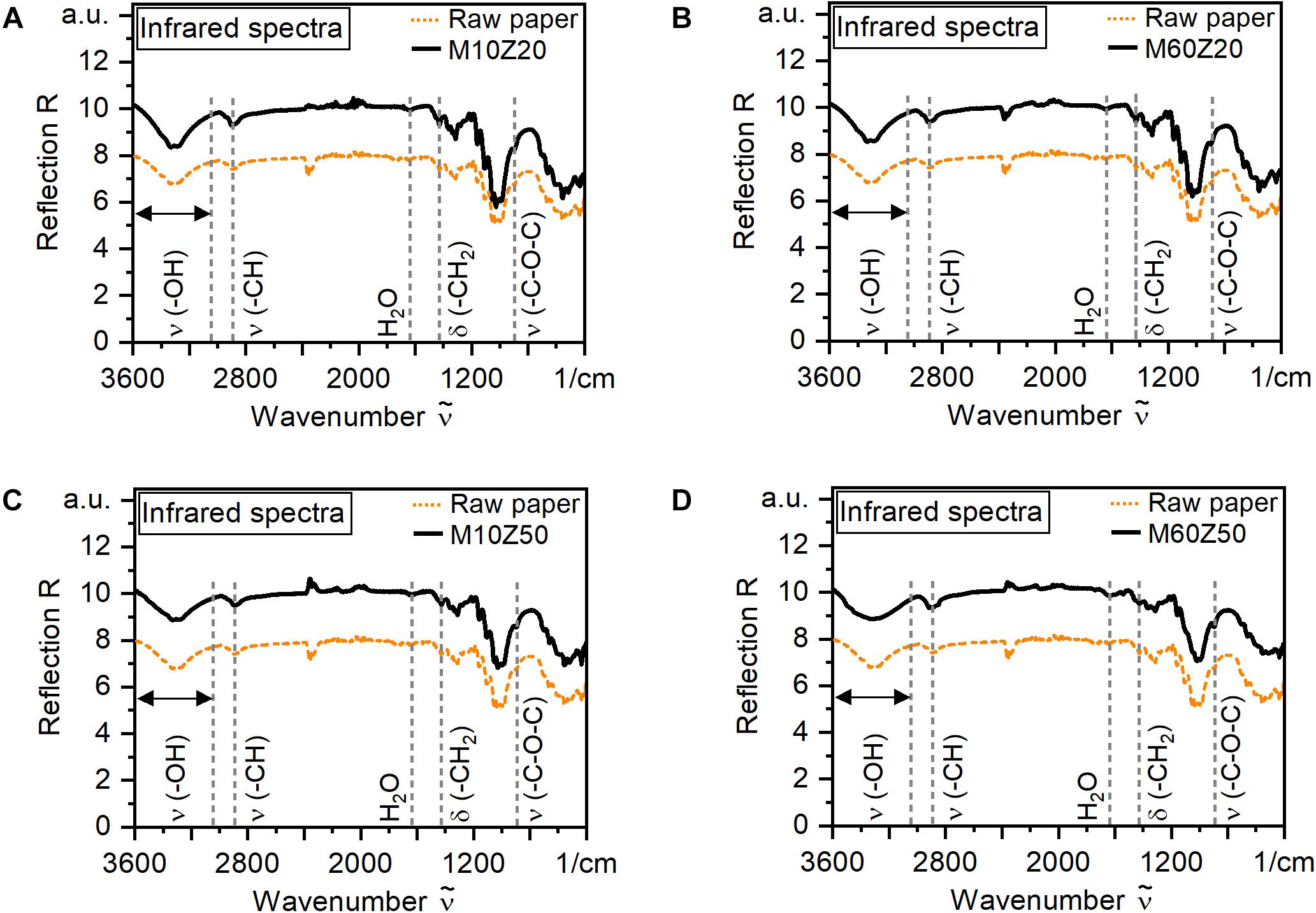
Figure 3. Infrared spectra with peak definition of raw paper M (Basis: cotton linters, Hahnemühle FineArt GmbH) and Cottonid variants (A) M10Z20, (B) M60Z20, (C) M10Z50, and (D) M60Z50.
By comparative evaluation of the spectra it becomes clear, that the basic structure of cellulose sustains the chemical treatment during parchmentizing as a step of the manufacturing process. Choosing a process temperature of Tcat,I = 20°C results in no distinct change in microstructure. Even when increasing the reaction time in the ZnCl2 solution to treact,II = 60 s, the spectra of M10Z20 in Figure 3A and M60Z20 in Figure 3B are nearly identical to the one of the raw paper M. With an increase of the process temperature to Tcat,II = 50°C changes can be seen concerning the peak in the interval from 3,600 to 3,100 cm–1 for M10Z50 in Figure 3C. The peak becomes more flat and wider. The change in this interval marks the modification of cellulose taking place during parchmentizing and indicates the formation of new inter- and intramolecular hydrogen bonds. This effect is even more significant for variant M60Z50 in Figure 3D with longer reaction time treact,II.
Figure 4A displayes obtained XRD patterns exemplary for M10Z20 and M60Z50. Whereas the pattern of M10Z20 is still characteristic for cellulose I, for M60Z20 and M10Z50 the intensity and sharpness of the marked peaks at 2θ = 18° and 2θ = 22° decrease with increasing reaction time treact and process temperature Tcat. The first significant changes could be obtained for M60Z50 (dotted green line). Here two new peaks occur at 2θ = 10.5° and in the range of 2θ = 18–20°. In Figure 4B the results of crystallinity determination based on IR spectra and XRD patterns for all Cottonid variants characterized in this study. Even if both methods show values that are very far apart, a relative decrease in crystallinity becomes clear with increasing process temperature Tcat and reaction time treact. With both measurements, a loss of crystallinity of about 25% from M10Z20 to M60Z50 in relation to raw paper M can be seen. It also underlines, that the influence of Tcat is more significant than the effect of treact.
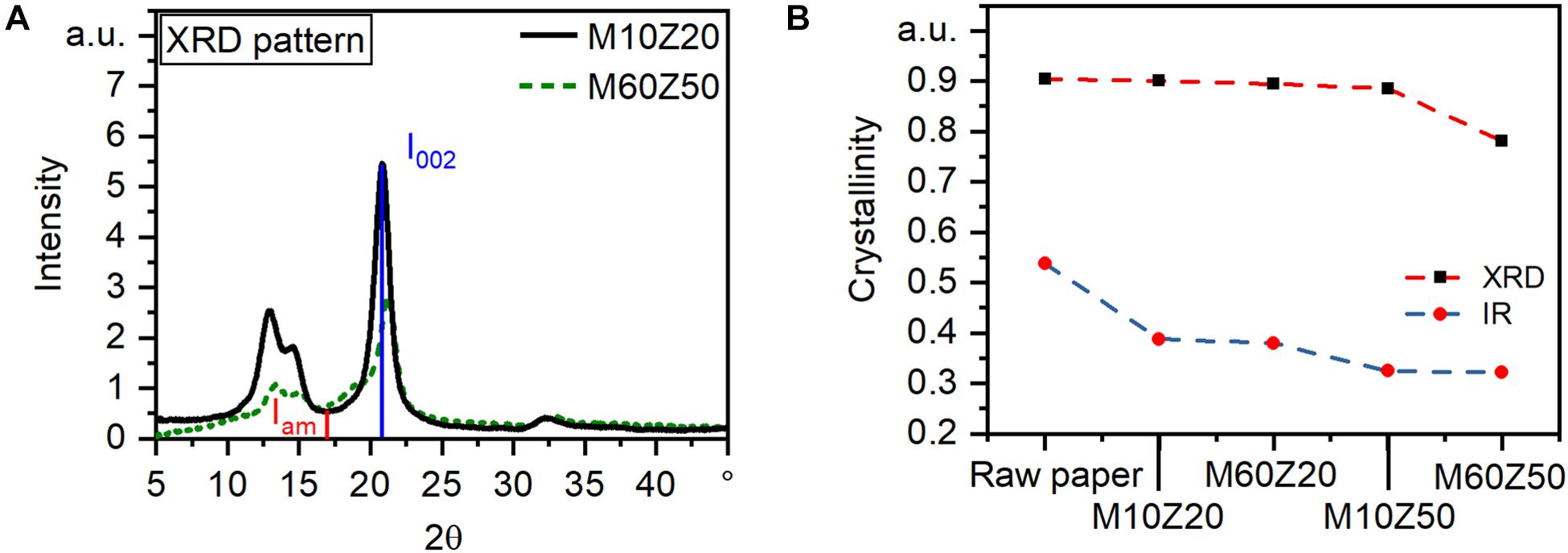
Figure 4. (A) Determination of crystallinity exemplary on XRD pattern of Cottonid variant M10Z20, (B) Cristallinity determined on the base of IR spectra and XRD patterns for all Cottonid variants.
Humidity-Driven Actuation
In Figure 5 the results of cyclic actuation experiments on the Cottonid variants (Figure 5A) M10Z20, (Figure 5B) M60Z20, (Figure 5C) M10Z50, and (Figure 5D) M60Z50 are shown. Deflection angle Δα as material reaction is plotted over the swelling time ts. Also shown are relative humidity φ as cyclic control parameter and temperature T as constant variable. The bilayered Cottonid/paper actuators are clamped at one side, whereas the hygro-sensitive Cottonid layer was on the bottom and more hygro-passive office paper on top. A positive Δα during the adsorption phase from φmin = 40% r.H. to φmax = 95% r.H. therefore represents a swelling of the Cottonid layer.
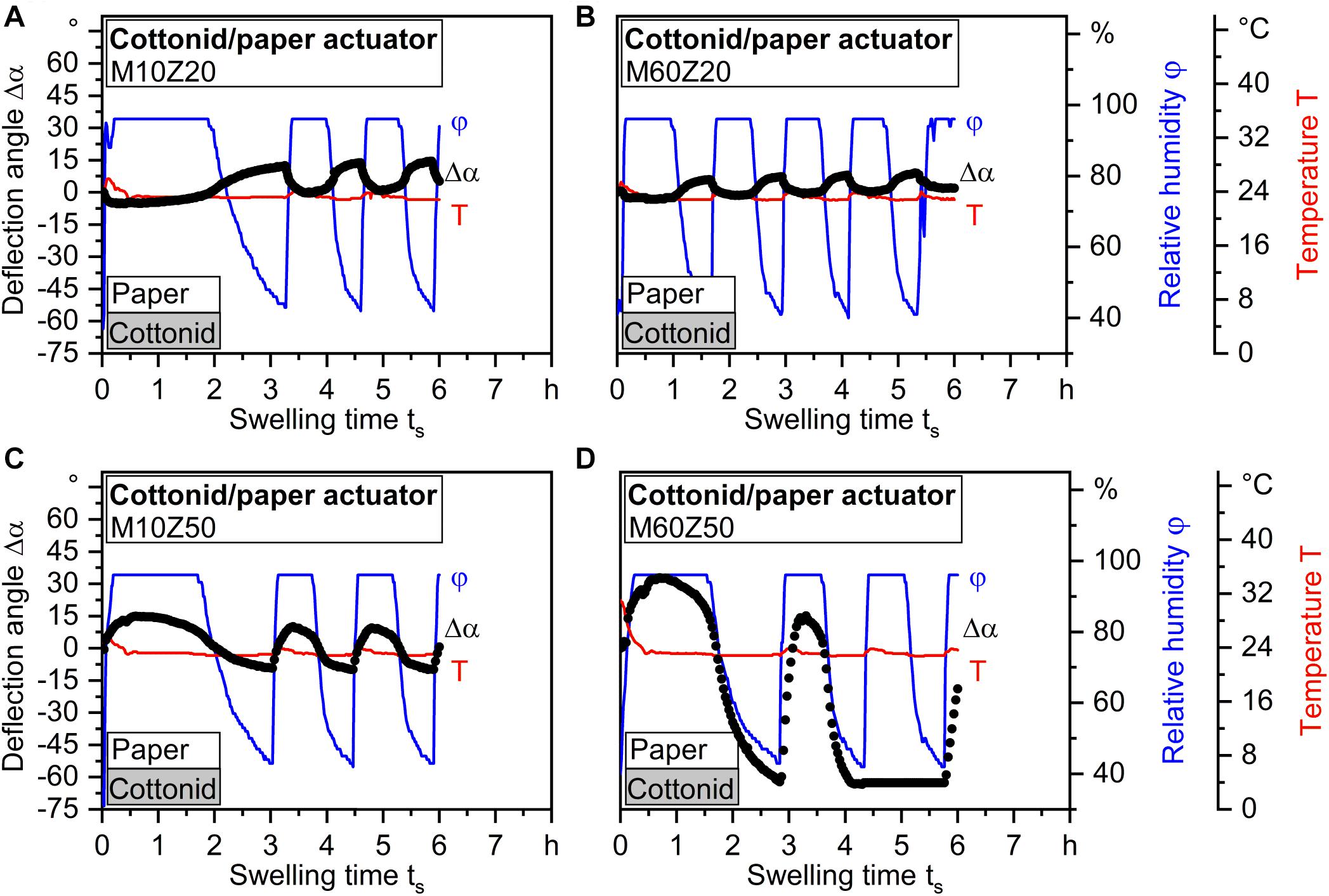
Figure 5. Cyclic actuation test (Deflection angle Δα vs. swelling time ts): (A) M10Z20, (B) M60Z20, (C) M10Z50, and (D) M60Z50.
When comparing the actuation curves it can be observed, that the M10Z20 and he M60Z20 bilayer actuators show an acyclic actuation behavior. When increasing φ, both specimens react with a negative Δα, which means, that the untreated office paper shows a stronger swelling and shrinking behavior than Cottonid. The relative deflection angle balances over the whole test duration are Δα10/20 = –19.8° and Δα60/20 = –12.3°. When looking at the variants with higher process temperature Tcat,II, as expected, when increasing relative humidity to φmax the M10Z50 and M60Z50 bilayer actuators show a positive Δα, so the Cottonid layer shows a stronger hygroscopic reaction than the untreated office paper layer. This effect is even more significant for variant M60Z50 in Figure 5D with longer reaction time treact,II. The relative deflection angle balances over the whole test duration are Δα10/50 = +24.9° and Δα60/50 = +96.1°.
Fatigue
Figure 6 displays the results of the fatigue investigations. In Figure 6A microstructural influences are focused and Cottonid specimens are tested in 0°, 45°, and 90° with regard to the manufacturing direction of the Cottonid sheet. Maximum stress σmax as control value is plotted over number of cycles N. As material reaction, maximum total strain εmax,t is shown. It can be seen, that different specimen orientations result in different maximum stresses σmax,f and maximum strains εmax,t,f at failure. As it was already shown by the authors in quasi-static investigations on industrial Cottonid material (Scholz et al., 2016), the specimen, which was prepared in manufacturing direction of the Cottonid sheet, shows highest values for σmax,f, whereas the specimen perpendicular to it shows the lowest one. The 45°-specimen lies between them. Table 2 sums up the obtained values. In Figure 6B environmental influences on the fatigue behavior of Cottonid are shown exemplary on 45°-specimens. It is clearly visible, that a high relative humidity of φhigh = 95% r.H. has a negative influence on the fatigue behavior, i.e., mechanical robustness during service loading. σmax,f,45,95 reaches ∼23.5% lower values than σmax,f,45,20. Figure 6C gives an insight in the integrated climate chamber with mounted fatigue specimen, where the speckle pattern for contact free strain measurement via DIC can be seen within the gauge length.
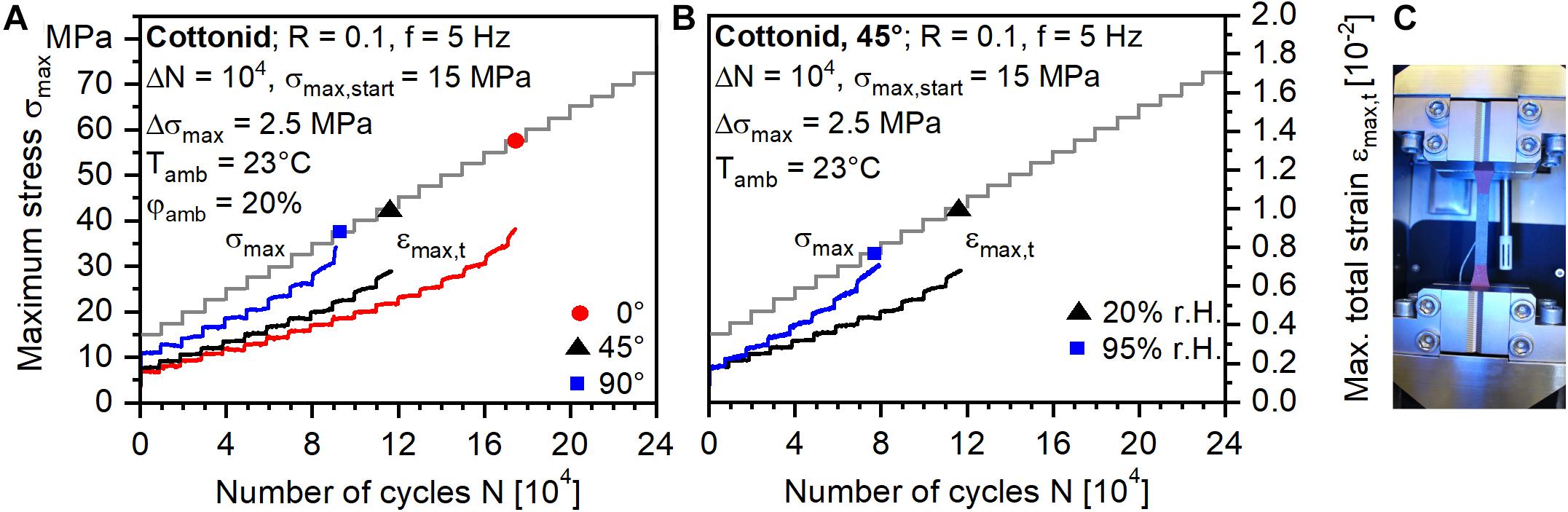
Figure 6. Results of multiple step test (MST): (A) Direction-dependent and (B) Humidity-dependent fatigue properties of Cottonid, (C) Mounted and instrumented fatigue specimen.
Discussion
The analysis of the structural investigations via SEM and IR spectroscopy leads to the conclusion, that the basic structure of cellulose is not affected by the chemical modification during parchmentizing. However, slight differences between the SEM micrographs and the IR spectra of the different Cottonid variants are present. When cellulose is exposed to a tempered catalyst both, the amorphous and crystalline regions are affected. The reduce of crystallinity becomes obvious through the visible microstructural linking of the cellulose micro fibrils, which correlates with changes in the IR spectra in the interval between 3,600 and 3,100 cm–1. The changes indicate the modification of cellulose taking place during the manufacturing process, which is characterized by formation of additional inter- and intramolecular hydrogen bonds. This also becomes clearer when evaluating the crystallinity determination using XRD and IR. The formation of new hydrogen bonds leads to an increase of the amorphous regions and therefore to a loss of crystallinity caused by the treatment with a tempered chemical catalyst. Since amorphous regions are essential for water uptake, the cellulose is now able to absorb more moisture from its environment, hence its hygroscopicity gets improved.
Accordingly, increasing the temperature of the catalyst bath by ΔTcat = 30 K, which leads to a stronger chemical reaction during manufacturing, has a positive effect on the actuation behavior of Cottonid. Bertran and Dale (1986) verified this phenomenon in their studies with differential scanning calorimetry on cellulose with different crystallinities. They came to the result, that hygroscopicity and crystallinity have a linear relation. So, the semi-crystalline cellulose I transforms within the parchmentizing process into another cellulose modification. The formation of two new peaks in the XRD pattern of M60Z50 in comparison to the other Cottonid variants investigated in this study underlines this statement. If the M60Z50 pattern is compared to simulated diffractographs according to French (2014) it can be assumed, that some parts of the cellulose I are transformed into cellulose II. The angular displacement of ∼1.5° is due to the sample height. That would mean, that Cottonid is a mixture of cellulose I and II. In this context (Schestakow et al., 2016) reported, that the mechanical properties of cellulose aerogels from aqueous zinc chloride solution have more in common with cellulose II aerogels from ionic liquids compared to aerogels made of other salt hydrate melts. Esch (2018) came to the same conclusion in her doctoral thesis, that cellulose II is formed, when treating cellulose I with a zinc chloride solution some cellulose II is formed.
The obtained fatigue properties of Cottonid are strongly dependent on the specimen location according to manufacturing direction of the Cottonid sheet, which is expressed by varying strength and deformation values at failure. Accompanying to the quasi-static investigations on industrial Cottonid material (Scholz et al., 2016), these observations verify the direction-dependent deformation behavior of Cottonid. This strong influence of the cellulose short fibers, which just have a predefined orientation due to the directed paper making process, can be exploited for a microstructural tuning of Cottonid to produce architectural components with complex adaptive deformation behavior. Further, the surrounding environmental conditions show a large influence on the mechanical strength. A high relative humidity, which ensures a pronounced actuation performance in case of humidity-adaptive elements, reduces the maximum stress at failure in the fatigue tests about 25%. Since mechanical robustness would also be an important factor when considering the material for architectural applications, these property-function relations have to be further investigated to identify ideal service conditions.
Summary and Outlook
In this study, the influence of manufacturing parameters, microstructural orientation as well as environmental factors on the actuation and fatigue performance of Cottonid was investigated. For that, different Cottonid variants were manufactured by varying process temperature Tcat as well as reaction time treact in the catalyst bath. Further, fatigue specimens were prepared in 0°, 45°, and 90° according to manufacturing direction of the Cottonid sheet and tested in varying environmental surroundings to assess the impact of microstructure and humidity on the mechanical robustness.
The variation of Tcat and treact resulted in Cottonid variants with significant differences in material properties. They differ concerning their microstructure, which is visible in the SEM micrographs as well as in the infrared spectra and XRD patterns. Further, it has an impact on the humidity-driven swelling and shrinking behavior. Generally it could be obtained, that Tcat is the decisive parameter. An increase about ΔTcat = 30 K has a positive effect on the actuation performance, whereas a too low process temperature seems to impair these properties. If Tcat is high enough, an increase of the reaction time treact is also beneficial for improving actuation performance. When Tcat is too low, an increase of treact shows no positive effect. With the results of XRD measurements in addition to SEM and IR spectroscopy and correlation with the actuation performance it could be proved, that a decrease of crystallinity through the formation of additional intra- and intermolecular hydrogen bonds, standing for an increase of amorphous areas, causes these findings. The next step is the investigation of fundamental mechanisms concerning transformation from cellulose I into cellulose II in aqueous zinc chloride solutions.
In fatigue experiments, specimens with varying microstructural orientation according to manufacturing direction show different cyclic strength and deformation values. This underlines the anisotropic behavior of Cottonid comparable to fiber-reinforced plastics, although the cellulose short fibers exhibit just a process-related predefined orientation. In addition, a high relative humidity has a negative influence on the mechanical robustness. This behavior can be exploited in the design of adaptive elements with programmed actuation performance via microstructural tuning. Since up to now mechanical tests were just performed on industrial material, the investigations will be repeated on the Cottonid variants I to IV (see Table 1).
In ongoing studies, the influence of further manufacturing parameters, like raw material for cellulose derivation, e.g., wood pulp instead of cotton linters, or chemical basis of the catalyst, e.g., sulfuric acid instead of zinc chloride solution, on the actuation and fatigue performance of Cottonid will be investigated. The obtained mechanical values serve further as a scientific basis for material-adapted modeling and prediction of deformations as a function of changing environmental parameters.
Data Availability Statement
The datasets generated for this study are available on request to the corresponding author.
Author Contributions
ML manufactured and provided the Cottonid variants and performed IR and XRD measurements. RS obtained SEM micrographs and performed actuation and fatigue experiments. RS and ML developed the testing procedure, prepared figures, and wrote the manuscript. CZ and FW supervised the project.
Funding
The authors thank the German Research Foundation (Deutsche Forschungsgemeinschaft, DFG) for funding the research project Biomechanical qualification of the structure-optimized functional material Cottonid as an adaptive element (WA 1672/23-1; ZO 113/22-1).
Conflict of Interest
The authors declare that the research was conducted in the absence of any commercial or financial relationships that could be construed as a potential conflict of interest.
Acknowledgments
We thank the Hahnmühle FineArt GmbH (Dassel, Germany) and the Ernst Krüger GmbH & Co., KG (Geldern, Germany) for providing raw material for Cottonid manufacturing and industrial reference material “Hornex.”
References
Bertran, M. S., and Dale, B. E. (1986). Determination of cellulose accessibility by differential scanning calorimetry. J. Appl. Poly. Sci. 32, 4241–4253. doi: 10.1002/app.1986.070320335
Ciolacu, D., Ciolacu, F., and Popa, V. I. (2011). Amorphous cellulose - structure and characterization. Cell. Chem. Technol. 45, 13–21.
Colombo, C., Harhash, M., Palkowski, H., and Vergani, L. (2018). Thermographic stepwise assessment of impact damage in sandwich panels. Composite Struct. 184, 279–287. doi: 10.1016/j.compstruct.2017.10.001
Colombo, C., Vergani, L., and Burman, M. (2012). Static and fatigue characterisation of new basalt fibre reinforced composites. Composite Struct. 94, 1165–1174. doi: 10.1016/j.compstruct.2011.10.007
Dai, M., Picot, O. T., Verjans, J. M. N., Haan, L., Schenning, A. P. H., Peijs, T., et al. (2013). Humidity-responsive bilayer actuators based on a liquid-crystalline polymer network. ACS Appl. Mater. Interf. 5, 4945–4950. doi: 10.1021/am400681z
Esch, K. (2018). Röntgendiffraktion An Papier und Vulkanfiber. Ph. D thesis, Technische Universität Dortmund, Dortmund.
Forterre, Y. (2013). Slow, fast and furious: understanding the physics of plant movements. J. Exp. Bot. 64, 4745–4760. doi: 10.1093/jxb/ert230
Fratzl, P., and Barth, F. G. (2009). Biomaterial systems for mechanosensing and actuation. Nature 462, 442–448. doi: 10.1038/nature08603
French, A. D. (2014). Idealized powder diffraction patterns for cellulose polymorphs. Cellulose 21, 885–896. doi: 10.1007/s10570-013-0030-4
Frey, M., Widner, D., Segmehl, J. S., Casdorff, K., Keplinger, T., and Burgert, I. (2018). Delignified and densified cellulose bulk materials with excellent tensile properties for sustainable engineering. ACS Appl. Mater. Interf. 10, 5030–5037. doi: 10.1021/acsami.7b18646
Grönquist, P., Wittel, F. K., and Rüggeberg, M. (2018). Modeling and design of thin bending wooden bilayers. PLoS One 13:e0205607. doi: 10.1371/journal.pone.0205607
Guiducci, L., Razghandi, K., Bertinetti, L., Turcaud, S., Rüggeberg, M., Weaver, J. C., et al. (2016). Honeycomb actuators inspired by the unfolding of ice plant seed capsules. PLoS One 11:e0163506. doi: 10.1371/journal.pone.0163506
Jedvert, K., and Heinze, T. (2017). Cellulose modification and shaping – a review. J. Poly. Eng. 37, 845–860. doi: 10.1515/polyeng-2016-0272
Markin, V. S., Volkov, A. G., and Jovanov, E. (2008). Active movements in plants: mechanism of trap closure by Dionaea muscipula ellis. Plant Signal. Behav. 3, 778–783. doi: 10.4161/psb.3.10.6041
Menges, A. (2012). Biomimetic design processes in architecture: morphogenetic and evolutionary computational design. Bioinspirat. Biomimet. 7:15003. doi: 10.1088/1748-3182/7/1/015003
Mittendorf, R.-M. (2016). Entwicklung einer Richtlinie Für Die Auslegung Von Direktschraubverbindungen In Vulkanfiber. Ph. D thesis, Technische Universität Dortmund, Dortmund.
Reyssat, E., and Mahadevan, L. (2009). Hygromorphs: from pine cones to biomimetic bilayers. J. R. Soc. Interf. 6, 951–957. doi: 10.1098/rsif.2009.0184
Rüggeberg, M., and Burgert, I. (2015). Bio-inspired wooden actuators for large scale applications. PLoS One 10:e0120718. doi: 10.1371/journal.pone.0120718
Schestakow, M., Karadagli, I., and Ratke, L. (2016). Cellulose aerogels prepared from an aqueous zinc chloride salt hydrate melt. Carbohyd. Poly. 137, 642–649. doi: 10.1016/j.carbpol.2015.10.097
Schmiedt-Kalenborn, A., Lingnau, L. A., Manka, M., Tillmann, W., and Walther, F. (2019). Fatigue and corrosion fatigue behaviour of brazed stainless steel joints AISI 304L/BAu-4 in synthetic exhaust gas condensate. Materials 12:1040. doi: 10.3390/ma12071040
Scholz, R., Langhansl, M., Zollfrank, C., and Walther, F. (2019a). “Cottonid – ein effizienter funktionswerkstoff für feuchtegetriebene aktuatoren,” in Proceedings of the Smarte Strukturen und Systeme – Tagungsband des 4Smarts-Symposiums, Munich.
Scholz, R., Langhansl, M., Zollfrank, C., and Walther, F. (2019b). Experimental study on the actuation and fatigue behavior of the biopolymeric material cottonid. Mater. Today Proc. 7, 476–483. doi: 10.1016/j.matpr.2018.11.112
Scholz, R., Mittendorf, R.-M., Engels, J. K., Hartmaier, A., Kuenne, B., and Walther, F. (2016). Direction-dependent mechanical characterization of cellulose-based composite vulcanized fiber. Mater. Test. 58, 813–817. doi: 10.3139/120.110929
Segal, L., Nelson, M. L., and Conrad, C. M. (1951). Experiments on the reduction of the crystallinity of cotton cellulose. J. Phys. Chem. 55, 325–336. doi: 10.1021/j150486a001
Shin, B., Ha, J., Lee, M., Park, K., Park, G. H., Choi, T. H., et al. (2018). Hygrobot. A self-locomotive ratcheted actuator powered by environmental humidity. Sci. Rob. 3:eaar2629. doi: 10.1126/scirobotics.aar2629
Taylor, T. (1871). Improvement in the Treatment Of Paper And Paper-Pulp. U.S. Patent No 114,880. Pittsburgh, PA: Unites States Patent Office. doi: 10.1126/scirobotics.aar2629
van Opdenbosch, D., Fritz-Popovski, G., Wagermaier, W., Paris, O., and Zollfrank, C. (2016). Moisture-driven ceramic bilayer actuators from a biotemplating approach. Adv. Mater. 28, 5235–5240. doi: 10.1002/adma.201600117
Vieweg, R., and Becker, E. (1965). Kunststoff-Handbuch Band III: Abgewandelte Naturstoffe:. Herstellung, Eigenschaften, Verarbeitung und Anwendung. München: Carl Hanser.
Keywords: Cottonid, bioinspired materials, microstructural tuning, cellulose modification, humidity-driven actuators, environmental fatigue, stimuli-responsive element production
Citation: Scholz R, Langhansl M, Zollfrank C and Walther F (2020) Humidity-Sensing Material Cottonid – Microstructural Tuning for Improved Actuation and Fatigue Performance. Front. Mater. 7:156. doi: 10.3389/fmats.2020.00156
Received: 01 July 2019; Accepted: 01 May 2020;
Published: 27 May 2020.
Edited by:
Laura Maria Vergani, Politecnico di Milano, ItalyReviewed by:
Raffaella Sesana, Politecnico di Torino, ItalyFrancesca Maria Curà, Politecnico di Torino, Italy
Copyright © 2020 Scholz, Langhansl, Zollfrank and Walther. This is an open-access article distributed under the terms of the Creative Commons Attribution License (CC BY). The use, distribution or reproduction in other forums is permitted, provided the original author(s) and the copyright owner(s) are credited and that the original publication in this journal is cited, in accordance with accepted academic practice. No use, distribution or reproduction is permitted which does not comply with these terms.
*Correspondence: Ronja Scholz, ronja.scholz@tu-dortmund.de