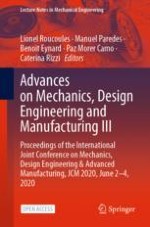
Open Access 2021 | OriginalPaper | Chapter
A New Smart Web Platform for Plastic Injection Molds in Industry 4.0 Environments
Authors : Cristina Martin-Doñate, Sliman Shaikheleid, Abelardo Torres-Alba, Jorge Manuel Mercado-Colmenero
Published in: Advances on Mechanics, Design Engineering and Manufacturing III
Publisher: Springer International Publishing
Activate our intelligent search to find suitable subject content or patents.
Select sections of text to find matching patents with Artificial Intelligence. powered by
Select sections of text to find additional relevant content using AI-assisted search. powered by