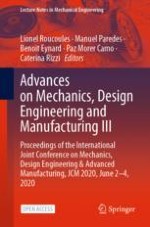
Open Access 2021 | OriginalPaper | Chapter
Customization of Kayak Paddle Grips by Using Reverse Engineering, Computer Aided Design and Additive Manufacturing Tools
Authors : Eneko Solaberrieta, Xabier Amezua, Xabier Garikano, Mikel Iturrate, Jose Antonio Oriozabala, Iñaki Martin
Published in: Advances on Mechanics, Design Engineering and Manufacturing III
Publisher: Springer International Publishing
Activate our intelligent search to find suitable subject content or patents.
Select sections of text to find matching patents with Artificial Intelligence. powered by
Select sections of text to find additional relevant content using AI-assisted search. powered by