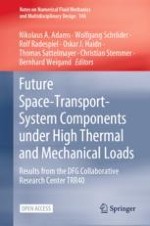
Open Access 2021 | OriginalPaper | Chapter
Dual-Bell Nozzle Design
Authors : Chloé Génin, Dirk Schneider, Ralf Stark
Published in: Future Space-Transport-System Components under High Thermal and Mechanical Loads
Publisher: Springer International Publishing
Activate our intelligent search to find suitable subject content or patents.
Select sections of text to find matching patents with Artificial Intelligence. powered by
Select sections of text to find additional relevant content using AI-assisted search. powered by