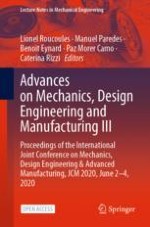
Open Access 2021 | OriginalPaper | Chapter
Modeling Symmetric Minimal Surfaces by Mesh Subdivision
Authors : Stefano Rosso, Andrea Curtarello, Federico Basana, Luca Grigolato, Roberto Meneghello, Gianmaria Concheri, Gianpaolo Savio
Published in: Advances on Mechanics, Design Engineering and Manufacturing III
Publisher: Springer International Publishing
Activate our intelligent search to find suitable subject content or patents.
Select sections of text to find matching patents with Artificial Intelligence. powered by
Select sections of text to find additional relevant content using AI-assisted search. powered by