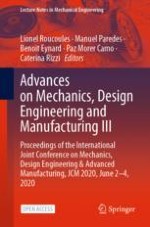
Open Access 2021 | OriginalPaper | Chapter
Numerical Simulation and Experimentation of Additive Manufacturing Processes with Polyurethane Foams
Authors : Elodie Paquet, Sébastien Le Loch, Benoit Furet, Alain Bernard, Sébastien Garnier
Published in: Advances on Mechanics, Design Engineering and Manufacturing III
Publisher: Springer International Publishing
Activate our intelligent search to find suitable subject content or patents.
Select sections of text to find matching patents with Artificial Intelligence. powered by
Select sections of text to find additional relevant content using AI-assisted search. powered by