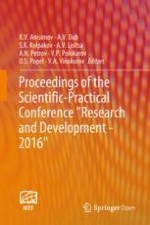
Open Access 2018 | OriginalPaper | Buchkapitel
Application of Volume-Surface Hardening by High-Speed Water Flow for Improving Static and Cyclic Strength of Large-Scale Castings from Low-Carbon Steel
verfasst von : S. A. Nikulin, A. B. Rozhnov, T. A. Nechaykina, V. I. Anikeenko, V. Yu. Turilina, S. O. Rogachev
Erschienen in: Proceedings of the Scientific-Practical Conference "Research and Development - 2016"
Aktivieren Sie unsere intelligente Suche, um passende Fachinhalte oder Patente zu finden.
Wählen Sie Textabschnitte aus um mit Künstlicher Intelligenz passenden Patente zu finden. powered by
Markieren Sie Textabschnitte, um KI-gestützt weitere passende Inhalte zu finden. powered by