Open Access 2016 | Open Access | Buch
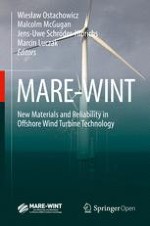
MARE-WINT
New Materials and Reliability in Offshore Wind Turbine Technology
herausgegeben von: Wiesław Ostachowicz, Malcolm McGugan, Jens-Uwe Schröder-Hinrichs, Marcin Luczak
Open Access 2016 | Open Access | Buch
herausgegeben von: Wiesław Ostachowicz, Malcolm McGugan, Jens-Uwe Schröder-Hinrichs, Marcin Luczak
This book provides a holistic, interdisciplinary overview of offshore wind energy, and is a must-read for advanced researchers. Topics, from the design and analysis of future turbines, to the decommissioning of wind farms, are covered. The scope of the work ranges from analytical, numerical and experimental advancements in structural and fluid mechanics, to novel developments in risk, safety & reliability engineering for offshore wind.The core objective of the current work is to make offshore wind energy more competitive, by improving the reliability, and operations and maintenance (O&M) strategies of wind turbines. The research was carried out under the auspices of the EU-funded project, MARE-WINT. The project provided a unique opportunity for a group of researchers to work closely together, undergo multidisciplinary doctoral training, and conduct research in the area of offshore wind energy generation. Contributions from expert, external authors are also included, and the complete work seeks to bridge the gap between research and a rapidly-evolving industry.